When it comes to manufacturing precise and durable components, there are several techniques available. However, one method that has gained popularity in recent years is lost-wax casting in stainless steel. This process involves creating wax patterns of the desired component, coating them with ceramic shell to create molds, and filling the molds with molten stainless steel. The result is a high-quality stainless steel component with intricate designs and exceptional corrosion resistance.

Key Takeaways:
- Stainless steel casting is a manufacturing method used to create precise and durable components.
- The lost-wax casting process involves creating wax patterns, coating them with ceramic shell, and filling them with molten stainless steel.
- Stainless steel components obtained through lost-wax casting are corrosion-resistant, strong, and versatile.
- Stainless steel casting is widely used in various fields, such as automotive, aerospace, and oil and gas industries.
- The lost-wax casting process allows for intricate designs and the use of molten stainless steel ensures strength and corrosion resistance.
The Lost-Wax Casting Process: Precision and Durability
At the heart of stainless steel casting lies the lost-wax casting process, a precise and intricate method of transforming wax patterns into durable stainless steel castings.
First, a wax pattern is created using either a manual or automated wax pattern injection press. This pattern is an exact replica of the final stainless steel casting to be produced.
The wax patterns are then coated in a refractory ceramic shell, creating a mold cavity, and heated to remove the wax, leaving behind a hollow ceramic mold.
Molten stainless steel is poured into the mold, filling the cavity and assuming the shape of the wax pattern. Once the metal solidifies, the ceramic shell is removed to reveal the final stainless steel casting.
The lost-wax casting process ensures precision in creating complex shapes and thin walls, resulting in high-quality stainless steel castings. The use of molten stainless steel ensures strength and durability, making these castings suitable for a variety of applications.
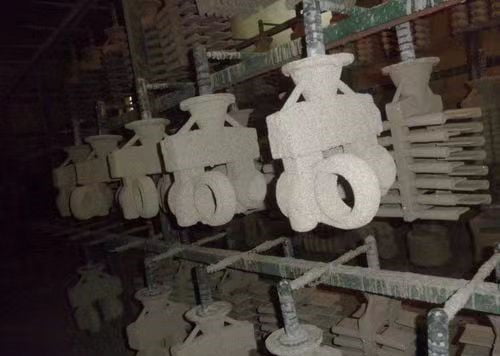
Lost-wax casting is a versatile casting process, allowing for the creation of stainless steel castings in various sizes and shapes. It is highly suitable for producing fine details, making it a popular choice for precision components in industries such as aerospace, healthcare, and automotive.
The lost-wax casting process is essential for the creation of precise and durable stainless steel castings. The use of molten stainless steel and the ability to create complex shapes and thin walls make this casting process ideal for a wide variety of applications.
Advantages of Stainless Steel Casting
At our stainless steel casting factories and companies, we specialize in final stainless steel castings using the investment casting process. This technique produces high-quality, intricate stainless steel components obtained through a mold cavity filled with molten stainless steel.
The advantages of using stainless steel casting are numerous. Firstly, stainless steel components have excellent corrosion resistance, making them ideal for use in harsh environments. Secondly, the investment casting process allows for complex shapes and thin walls to be achieved, resulting in lightweight yet strong components.
Furthermore, stainless steel casting is a versatile manufacturing method that can be applied across a wide range of industries, from automotive and aerospace to medical and energy. It is particularly useful in the oil and gas industry, where components must withstand extreme temperatures and pressures.
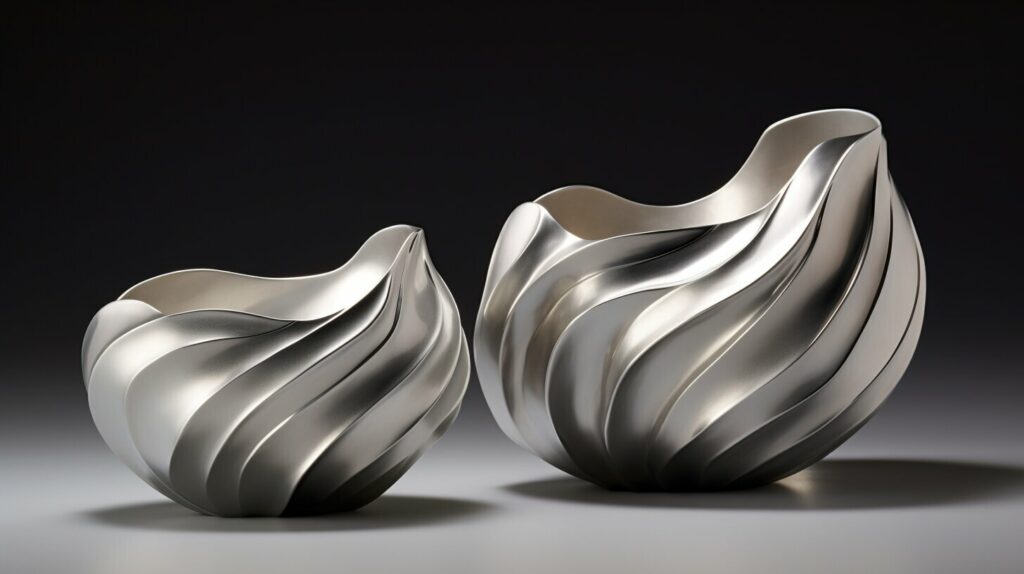
The use of stainless steel casting also reduces the need for post-production machining, as components can be cast to near-net shape. This results in cost savings and a faster turnaround time, making it a cost-effective solution for many applications.
Our stainless steel casting factories and companies are equipped with state-of-the-art technology and highly skilled technicians, ensuring precision and consistency in every cast. We take pride in our ability to produce high-quality stainless steel components that meet the exact specifications of our clients.
The Process: From Wax Patterns to Finished Castings
Stainless steel casting involves several intricate steps that require precision and attention to detail to achieve optimal results. The lost-wax casting process is used to create molds that will produce the final stainless steel castings.
First, a ceramic shell is created by dipping the wax pattern in a ceramic slurry and then drying it. This process is repeated multiple times until a thick and sturdy shell is formed. The ceramic shell is then put in a kiln, which melts the wax and leaves behind a mold cavity.
Next, the molten stainless steel is poured into the mold cavity through a wax pattern injection press. The press uses a hydraulic system to force hot molten metal into the ceramic shell and fill the mold. After a cooling period, the ceramic shell is broken away, revealing the final stainless steel casting.
Coating wax patterns with ceramic shells ensures that the final product will be precise and durable. Wax removal is a critical step in creating the mold cavity, and it must be done carefully to avoid damaging the ceramic shell. The corrosion resistance of stainless steel castings is one of the many advantages of using this casting process.
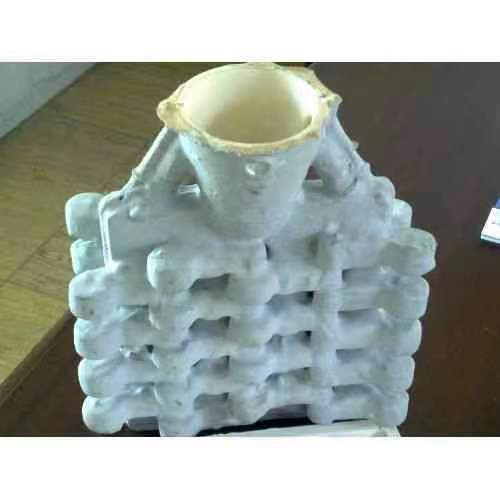
The lost-wax casting process is a delicate and intricate process, but it is well worth the effort to achieve the precise and durable stainless steel components that are obtained.
Applications and Industries for Stainless Steel Casting
Stainless steel casting has a wide range of applications across various industries. From large to small stainless steel castings, this manufacturing process is relied upon for creating durable and precise metal components.
In the oil and gas industry, stainless steel castings are used in a range of equipment, including valves, pipes, and pumps. These components must withstand high temperatures, pressures, and corrosive environments. As such, stainless steel castings are the ideal choice for the industry due to their heat and corrosion resistance, ensuring reliability and longevity of the equipment.
The versatility and strength of stainless steel casting also make it a popular choice in the automotive industry. Large and small stainless steel castings are used in various components such as engine parts, gearbox casings, and suspension parts. The use of stainless steel ensures high strength and durability, making it a reliable choice for these critical components.
Beyond these heavy industries, stainless steel castings are used in a wide range of applications, from electrical components to kitchen utensils. One unique application is in the insulation heat preservation box industry. Small stainless steel castings are used to create the hinges and latches that secure these boxes, ensuring that heat is retained and food is kept fresh.
As evident from these examples, the applications of lost wax casting in stainless steel are vast and varied. The ability to create complex shapes and thin walls allows for intricate designs, while the strength and heat resistance of the final stainless steel castings make them a reliable choice for a multitude of industries.
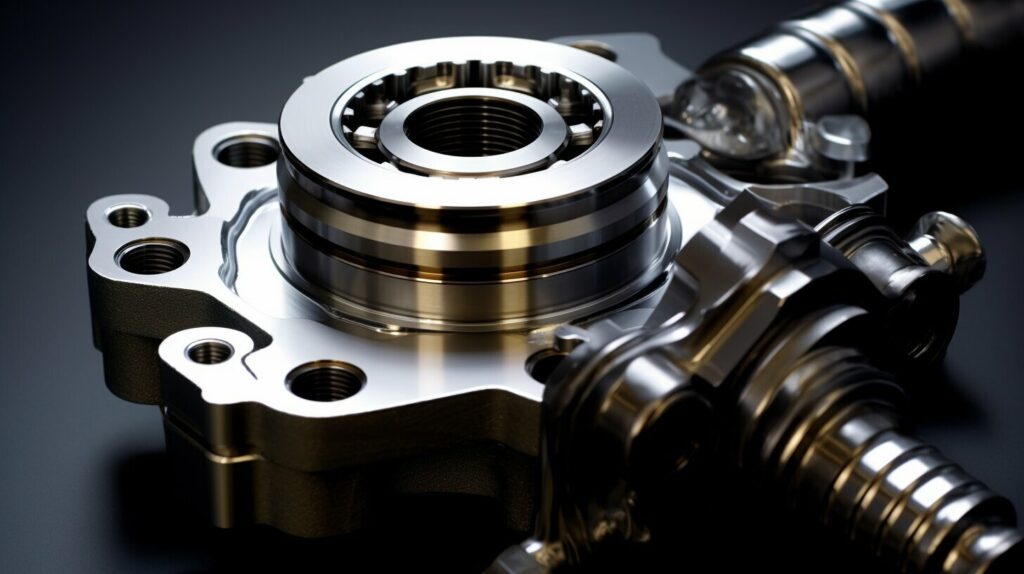
“The ability to produce high-quality stainless steel castings in a range of sizes and shapes makes it a reliable choice for industries seeking durable and precise metal components.”
Key Factors to Consider in Stainless Steel Lost Wax Casting
If you are considering using stainless steel lost wax casting for your next project, there are a few key factors that you need to take into account. Here are some of the most important things to keep in mind:
The first thing you need to know is what grade of stainless steel you will need. There are many different grades available, each with its own set of benefits and drawbacks. The most important thing is to choose a grade that is appropriate for the application.
The next thing to consider is the size and shape of the component. This will determine the size and shape of the wax pattern. It is important to make sure that the wax pattern is the correct size and shape, as this will affect the final casting.
The last thing to consider is the surface finish. This is important because the surface finish will determine the amount of time and effort required to polish the final casting. If you want a high quality surface finish, you will need to use a higher grade of stainless steel.
Conclusion: Unlock the Potential of Stainless Steel Casting
At our stainless steel casting factories, we believe that the lost-wax casting process offers unparalleled precision and durability. By transforming wax patterns into final stainless steel castings through the use of molds and molten stainless steel, we can create complex shapes and thin walls with ease. These durable and corrosion-resistant components offer strength and versatility to a wide range of industries.
From automotive to aerospace, oil and gas to insulation heat preservation box, stainless steel castings have diverse applications. The ability to create large and small stainless steel castings with intricate designs and superior heat resistance makes stainless steel casting a versatile choice for industries seeking high-quality metal components.
Unlocking the Potential of Stainless Steel Casting
Stainless steel casting offers a wealth of possibilities for creating precise and durable components. The lost-wax casting process allows for intricate designs and the use of molten stainless steel ensures strength and corrosion resistance. With its wide range of applications and advantages, stainless steel casting is a versatile choice for industries seeking high-quality metal components. At our stainless steel casting companies, we strive to unlock the full potential of this manufacturing method and provide our clients with top-of-the-line stainless steel components that meet their specific needs and requirements.
Whether you need large or small stainless steel castings, our investment casting process can deliver the perfect solution for your industry. Contact us today to learn more about the process and how we can help you optimize your manufacturing process with precision and durability.
At KT-Foundry, we grasp the significance of precision and meticulousness in crafting tailored castings for our valued clients. Our team comprises seasoned engineers and skilled technicians who leverage cutting-edge technology and advanced techniques to ensure that each casting aligns with your exact specifications.
FAQ
Q: What is lost-wax casting?
A: Lost-wax casting is a manufacturing process that involves creating a wax pattern, coating it with ceramic material, and then melting away the wax to create a mold. Molten stainless steel is poured into the mold, creating a precise and durable stainless steel component.
Q: What are the advantages of using lost-wax casting for stainless steel?
A: Lost-wax casting allows for the creation of complex shapes and thin walls, resulting in versatile and strong stainless steel components. The process also ensures precise dimensions and excellent surface finish. Additionally, stainless steel castings are resistant to corrosion and can be used in various industries.
Q: Which industries can benefit from stainless steel casting?
A: Stainless steel casting has wide-ranging applications in industries such as automotive, aerospace, oil and gas, and more. It is used to create components for engines, pumps, valves, turbines, and other equipment that require strength, durability, and resistance to extreme conditions.
Q: How does the lost-wax casting process work?
A: The lost-wax casting process starts with the creation of a wax pattern through injection molding. The wax patterns are then coated with ceramic material to create a mold. The wax is melted away, leaving behind a cavity. Molten stainless steel is poured into the mold, filling the cavity. After solidification, the ceramic shell is broken away, revealing the finished stainless steel casting.
Q: What are the benefits of using stainless steel castings?
A: Stainless steel castings offer a range of benefits, including high strength, corrosion resistance, and the ability to withstand extreme temperatures. They can be used in demanding environments and are known for their longevity and low maintenance requirements.
Q: Are there size limitations to stainless steel castings?
A: Stainless steel castings can be produced in a wide range of sizes, from small intricate components to large and complex structures. The versatility of the lost-wax casting process allows for the creation of various sizes and shapes to meet specific application requirements.