One of the key elements of a successful casting industry is pattern-making. The final output of the metal casting will look like the sand casting patterns. It is also used to create mold. The pattern material is typically made from wood, metal, plastic, or wax, and they are usually coated with a release agent to ensure that the sand does not stick to the pattern surface.
The casting pattern must be designed carefully to ensure that the finished product meets the desired specifications.
How Sand Casting Patterns Are Made
Sand casting is a manufacturing process where molten metal is poured into a sand mold. The process involves creating a pattern in the sand, which is used as a template for the liquid metal to flow into and form the desired shape.
Pattern-making is done by compacting sand into the desired shape using wooden or metal patterns. The patterns are placed into the sand and then compacted with a ramming tool.
3D Printing
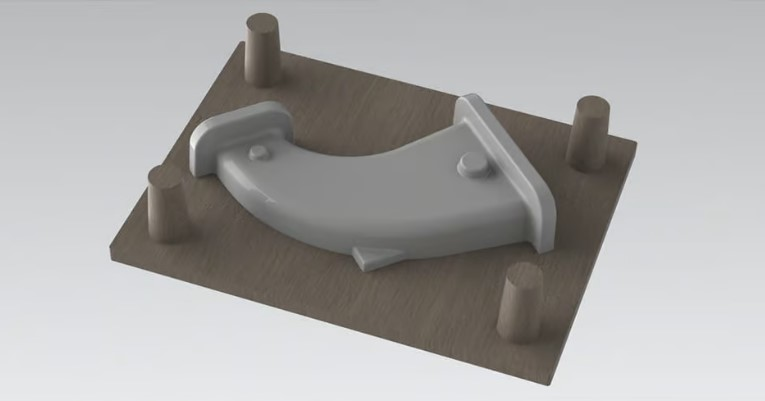
This has brought a new level of accuracy and efficiency to the casting process. The process begins with the creation of a 3D model of the final product, which is then converted into a printable file.
This file is then sent to a 3D printer, and layers of a specialized sand-like material are made for 3d printing. The pattern is then removed from the printer and cured, resulting in an accurate and detailed pattern that can be used for sand casting.
3D-printed sand casting patterns offer a number of advantages over traditional methods. For one, they are less expensive and require less labor.
Sand Casting Patterns Where a Molten Metal is Poured
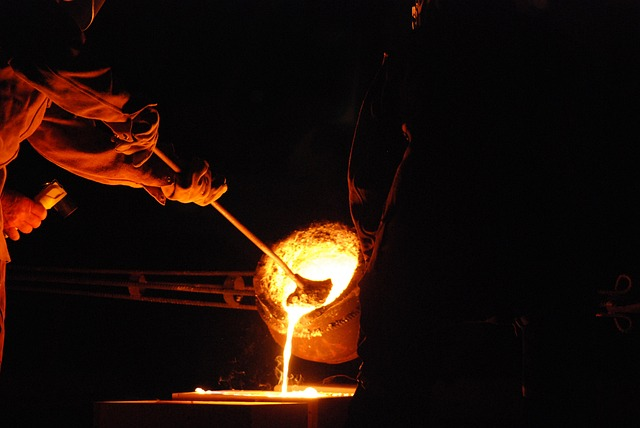
Patterns are made out of a variety of materials, including wood, metal, plastic, and even cardboard.
Wax Patterns
A wax pattern is an essential part of the manufacturing processes of castings, including investment casting and sand casting. The wax is heated and poured into a mold, where it hardens into the desired shape.
To create the sand casting, the wax pattern is placed into a container filled with sand. The sand molds will follow the shape and size of the wax pattern.
Wax patterns are often used in the sand casting process because they are relatively inexpensive, easy to make, and can be reused. Additionally, the wax pattern can be modified or changed to create different designs and shapes. Wax patterns are also very accurate, as they can be measured to the desired casting and accurate dimensions.
Patterns Made of Wood
A wood pattern is relatively lightweight and can be easily handled and transported.
When choosing a block of wood for pattern making, it is important to consider the type of wood, the grain pattern, the wood’s stability, and the type of finish it will require. Generally, hardwoods such as oak, maple, and birch are the best choices for a sand-casting pattern.
Softwoods, such as pine and cedar, are not recommended for patterns, as they are more likely to warp and deform when exposed to the high temperatures of the casting process of metal parts.
Plastic Patterns
Plastic patterns are used to form the cavity in the sand mold that is used to create the desired shape of the metal part. The patterns are typically made from a plastic material such as ABS or polyurethane.
These materials are lightweight, durable, and easy to work with, making them ideal for sand casting processes. They also have a low melting point, so they can be melted down and reused for future casting design.
The plastic pattern is created using a CAD program, which allows the designer to create a detailed 3D model of the desired shape. This model is then used to create a master pattern, which is used to make the patterns that will be used to cast metal.
These patterns can be customized to include any details or features that are needed to create the perfect part.
Types of Patterns for Sand Casting Process
Gated Patterns
The gated pattern is typically created by using a series of grooves, which are cut into the mold using a special tool. The grooves are cut in a specific configuration, which allows the metal to flow evenly throughout the mold, ensuring that the cast shape is even and free of defects.
In the gating system, the pattern is placed into the sand, and channels are then cut into the sand. These channels create a pathway for the metal to flow. The channels are typically cut in a specific pattern, known as a gated patterns, to ensure that the liquid metal is evenly distributed throughout the mold.
Gating systems ensure that the liquid metal is evenly distributed throughout the sand molding, resulting in a quality solid metal. In addition, it also helps to prevent air pockets from forming, which can cause defects in the final cast shape.
By understanding and utilizing the proper gating techniques, you can ensure that the final product is of the highest quality.
Cope and Drag Patterns
Cope and drag patterns are the two halves of a sand casting mold. The cope is the top section of the mold and has dowel pins. The drag is the bottom section. The two halves form the complete mold when they are put together, with the drag pattern nested inside the cope.
Each half of the mold contains a cavity that replicates the shape of the finished casting. The cavity is created by cutting the pattern into the sand and filling the space with a binder.
The cope and drag patterns must be designed in such a way that the liquid metal can be poured into the mold and cooled without any problems. The patterns must also be designed with pattern allowances when the liquid metal to expands during cooling.
Match Plate Patterns
Match plates are made from a pattern that is cut into two halves, which are then placed onto the sand mold. These are two-sided patterns that are used to create a three-dimensional shape in creating metal parts. The two sides of the pattern are typically identical, and the shape is created by filling the space between the two sides with sand.
These parts are used in a range of industries, from automotive to aerospace. The match plate pattern is placed into the sand molding and then filled with liquid metal. This allows for parts with high levels of accuracy.
When creating a match plate pattern, metal choice will affect the melting temperature and the strength of the metal. The shape of the casting will affect the amount of material required and the complexity of the pattern.
The size of the casting will determine the amount of sand that must be used to fill the space between the two sides. The surface finish will determine the amount of time and effort required to achieve a smooth and even finish.
Skeleton Patterns
Skeleton patterns are an important part of the process. These patterns are used to create a hollow space or void in the center of the casting. This void is then filled with liquid metal and left to cool. The skeleton pattern not only creates the desired shape but also helps to reduce the cost of production.
It is used to form the mold cavity, which is then filled with liquid metal. The skeleton pattern is placed inside the mold and held in place with pins or other holding devices.
The pattern is created by assembling a series of ribs and joints that make up the shape of the casting. The ribs and joints are connected by pins and screws, creating the desired shape. The pattern is then placed in a sand box and the sand is packed around it.
Shell Patterns
Shell patterns offer several advantages over traditional sand casting. The thin shells create a more accurate shape than thicker molds, and the hollow shells reduce the overall weight of the part. Shell patterns also offer improved strength and durability, as the parts created are more resistant to cracking and warping.
These are commonly used in the production of automotive parts, sporting goods, and industrial components, and other production parts. While the shell pattern process is more expensive than traditional sand casting, it can produce parts that are more accurate and durable.
Loose Patterns
Loose patterns are the core of the process and are used to create the internal structure of the part. The pattern is made from a variety of materials including wood, plastic, and metal and is used to form the mold cavity.
The patterns used in sand casting are not rigidly fixed in place, hence the term “loose pattern.” The pattern is actually loose inside the flask, allowing for some movement during the pouring process. This movement allows for the molten metal to flow evenly throughout the mold cavity and create a consistent product.
Loose patterns are an essential part of sand casting, and their use is critical to achieving success. Without the use of loose patterns, the molten metal would not flow evenly, and the final product would not be as accurate as desired.
Sweep Patterns
A sweep pattern is created using a variety of methods, such as manual carving, computer-aided design (CAD) software, and 3D printing. The pattern is designed to create the desired shape and design of the object and is typically created by a skilled pattern maker.
It is typically made of metal, wood, or plastic. The pattern is removed from the mold, and the finished cast can then be machined and finished.
Allowances Needed in the Casting Patterns
Allowances refer to the extra space provided inside the patterns to compensate for contraction of the metal during when exposed to a cooler temperature. Without this allowance, the metal may not fit into the pattern.
It is important to understand the different types of allowances and how they affect the process in order to achieve the desired results during the finishing stage.
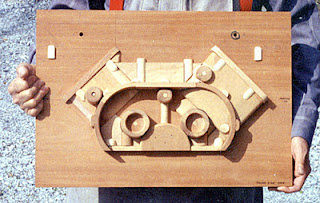
Machining Allowance
The most important aspect of machining allowances is their ability to compensate for any errors that may occur during the machining process. This includes any discrepancies that may arise between the pattern and the finished product due to shrinkage or other factors.
By allowing for additional material in the pattern, machining allowance can help to ensure that the finished product is as close to the intended design as possible.
Distortion Allowance
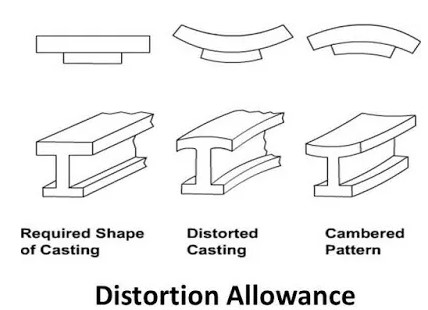
Distortion allowances are an allowance made to the pattern to account for any expected cooling distortion that may occur during the casting process. They are usually expressed as a percentage of the overall pattern dimension. The amount of allowance required depends on the type of process being used, as well as the material and complexity of the part.
In general, an allowance of 0.5 to 2% is used for sand casting patterns. This allows for some flexibility in the finished part, and prevents the need for excessive machining to correct any initially distorting parts. However, if a higher degree of accuracy is required, a higher allowance may be necessary.
The type of sand used in the mold can also affect the amount of distortion allowance required. Coarser sands are more prone to distortion, while finer sands tend to be more stable.
Shrinkage Allowance
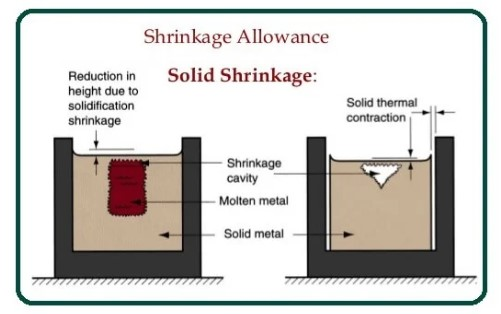
The amount of shrinkage allowance will vary depending on the type of metal being cast and the size of the part being cast. In general, the larger the part, the greater the shrinkage allowance.
When incorporating shrinkage allowances into a sand casting pattern, it is important to take into account the type of metal being cast. Different metals have different shrinkage rates, so it is important to use the correct allowance for the specific metal being cast.
It is important to note that shrinkage allowances should not be too small or too large. If the allowance is too small, the part will not be the correct size, and if it is too large, the part will be too big.
In general, the larger the part, the greater the allowance. The shrinkage allowance compensates the metal’s space to cool and contract as it solidifies.
Contraction Allowance
The purpose of adding contraction allowances to the pattern is to ensure that the final casting will be the exact size that was intended. Without the allowances, the casting could end up being too small due to the metal shrinking during cooling. This could cause the part to be unusable or require additional machining work to make it fit the intended design.
Adding contraction allowances to patterns also helps to reduce the excess material of scrap metal produced during the process.