Shell molding casting is an excellent choice for producing precision parts with complex geometries. It allows for intricate designs to be created with minimal waste. It is a popular choice for producing intricate castings in a wide variety of materials, including aluminum, brass, bronze, and more.
This process is a popular choice for the production of complex, thin shell walls, and highly detailed components, as it provides excellent surface finish, dimensional accuracy, and a wide range of alloy capabilities.
Understanding The Shell Mold Casting
The shell casting process is relatively simple and efficient, and it produces high-quality parts with excellent surface finish and dimensional accuracy. It is used in casting reactive materials, such as aluminum and magnesium alloys.
The process is well suited to producing complex shapes and intricate details and is capable of producing high-quality parts with a significantly reduced lead time.
The shell halves are usually made of a ceramic slurry, which is poured into a mold or box and allowed to dry. The thin-walled shell created is then dipped into a liquid plastic resin binder, which hardens around it. Once the shell is complete, it is removed and the core is discarded.
How Shell Mold Casting Process is Done
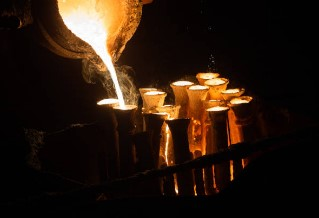
The shell mold casting process involves the use of a resin-coated sand-based mold, where molten metal is poured to create the shape of the desired metal component.
The pattern is typically made of wood or plastic, and it is used to create a negative impression of the part in the shell mold. The negative impression of the part is what will become the actual metal pattern.
Once the pattern is complete, it is placed in a flask with a backing material, which is a special container that holds the sand resin mixture used to create the mold. The sand is then compressed around the pattern using a special machine known as a rammer. The rammer applies pressure to the sand casting, which is then packed tightly around the pattern.
Once the sand has been packed tightly around the pattern, it is then covered with a thin-walled shell material. The hardened shell is usually made of a ceramic material, such as alumina, and it provides a strong, durable surface for the mold.
The shell material is then heated to a high temperature, which creates the complete shell mold. The molten metal can be any type of alloy steel, such as carbon steel and aluminum.
Depending on the type of alloy steel used, this can take anywhere from a few minutes to several hours. Once the metal has cooled, the half and surrounding shell can be destroyed to bring out the metal casting. Any excess metal can be trimmed away and the part can be finished as desired.
Materials Used for Shell Molding Process
The materials used to create shell molding vary depending on the application. Other materials such as alumina, chromite, and zircon are also used for specific applications.
The heated metal pattern is the other material used in creating the two shell halves. It is heated to ensure that the heated pattern partially cures and the pattern leaves a detailed impression on the sand.
Benefits of Using Shell Molds in a Casting Process
One of the main advantages of using shell mold in sand casting is that they provide a high level of accuracy and detail. This is because the molds are created using uniform and finer sand.
The sand also helps to reduce the chances of shrinkage or create a very smooth surface for the metal component.
The molds are relatively inexpensive to produce and can be reused to form multiple shell molds, which helps to reduce the overall cost of the cast iron process.
Additionally, the molds are relatively easy to create and maintain, making them a great option for companies who are looking to reduce their costs.
Disadvantages of Using Shell Molds in Metal Casting Process
The shell mold casting must be filled with a liquid ceramic slurry, which can cause the mold to break down over time. This can lead to inconsistencies in the casting process and can increase the time of production.
Because the molds are made of a mixture of sand and a binder, they can be difficult to shape into the desired form. This can make it difficult to get the desired result.
Where Shell Mold Casting Process is Used
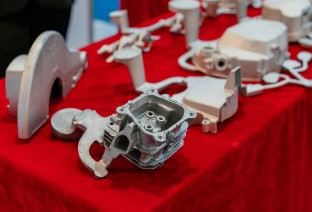
The process is often used to create automotive parts such as gear housings, engine blocks, cylinder heads connecting rods, and other engine components.
It is also used to produce aerospace components such as lever arms, landing gear, turbine blades, and other precision parts. In the medical field, shell mold casting is used to create implants such as dental crowns and hip replacements.
The process is more efficient than other casting methods, as it uses fewer steps and requires less labor. The process is also capable of producing large quantities of parts quickly and reliably.