Metallurgical analysis plays a vital role in the study of various physical and chemical behaviors of metallic elements, paving the way for creating high-quality metal alloys suitable for a wide range of consumer and manufacturer applications. It involves a meticulous process of sample preparation methods, testing methods for evaluating samples’ suitability for their intended purpose, and metallography to examine microstructures and understand the effects of different manufacturing processes like thermal, forming, joining, and more. In this comprehensive guide, we will delve deeper into the process and importance of metallurgical analysis in carbon steel casting, exploring its significance in material science and manufacturing processes.
Key Takeaways
- Metallurgical analysis is crucial for understanding the properties and behavior of metal alloys, like carbon steel casting.
- Various testing methods are employed to study the properties and suitability of metal alloys for different applications.
- Microstructure examination is essential for determining factors like grain size, inclusion content, and phase distribution in carbon steel casting.
- Strict quality control and rigorous testing standards are necessary for ensuring the highest quality of carbon steel castings.
- Advanced metallurgical testing methods allow foundries like KT-Foundry to optimize casting processes and create durable, reliable metal components in various industries.
Understanding the Significance of Metallurgical Analysis in Carbon Steels
Metallurgical analysis of carbon steel is central to understanding its chemical, physical, and mechanical properties. By observing prepared specimens at the micro and macro levels, analysts can evaluate critical factors such as grain size, inclusion content, phase distribution, and porosity. Such analysis traces back to early science, with roots deepening in the industrial revolution, requiring a sophisticated understanding of metal properties to produce consistent, high-quality goods. Today, it plays a significant role in various industries, including automotive, transportation, and medical devices, to meet specific manufacturing specifications.
To fully appreciate the significance of metallurgical analysis in carbon steel, let’s explore the impact of this examination on the study of microstructure observation, understanding of carbon steel properties, and identification of various steel alloys.
Metallurgical analysis not only strengthens our knowledge of carbon steel, but it also lays the foundation for improved manufacturing processes and enhanced material capabilities.
The following table reveals essential aspects of carbon steel metallurgical analysis, emphasizing its importance in determining the properties and applications of carbon steel:
Aspects of Analysis | Role in Carbon Steel Properties | Impact on Applications |
---|---|---|
Grain size | Determines strength, ductility, and hardness | Influences material behavior under stress, wear, and fatigue |
Inclusion content | Impacts mechanical properties and internal structure | Affects material performance and durability |
Phase distribution | Deciphering the different metallurgical phases within the material | Informs heat treatment processes and material capabilities |
Porosity | Highlights potential areas of weakness and internal integrity | Guides casting quality and potential for machining |
To ensure accurate analysis and interpretation, a variety of testing standards and methods have been established. Comprehending these procedures is imperative for maintaining the production of high-quality carbon steel components across multiple industries.
- ASTM E112: Standard test method for determining grain size
- ASTM E45: Standard test method for determining inclusion content
- ASTM E340: Standard practice for the evaluation of phase distribution
In conclusion, the significance of metallurgical analysis in carbon steel plays a critical role in driving advancements within the manufacturing sector, improving material capabilities, and ensuring the development of high-performance products. This intricate study of microstructure, carbon steel properties, and steel alloys has laid the groundwork for exceptional progress across various industries, shaping the world as we know it.
The Role of Microstructure Examination in Carbon Steel Casting
Microstructure examination plays a crucial role in carbon steel casting, as it directly relates to properties such as strength, ductility, and hardness. Understanding and assessing grain size, phase distribution, and identifying inclusions and segregation are essential elements in determining the material’s final properties. Through metallography and various ASTM standards, the examination provides valuable insights into the suitability of the metal for its desired application.
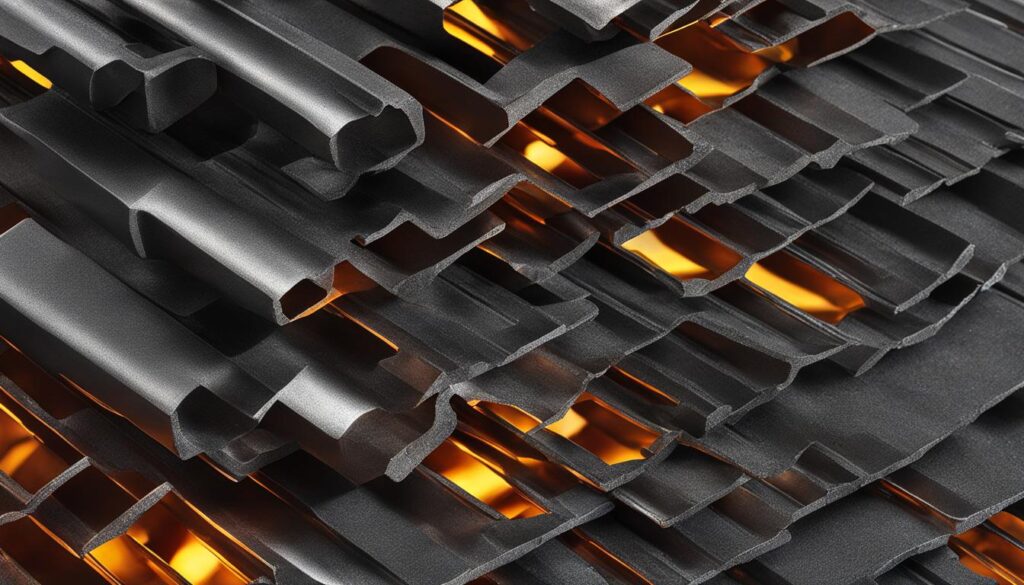
Techniques for Assessing Grain Size and Phase Distribution
Grain size assessment and phase distribution analysis are fundamental aspects of microstructure examination. By utilizing ASTM E112 for grain size assessment, it becomes possible to estimate the metal’s mechanical properties, such as fatigue strength and corrosion resistance. Furthermore, ASTM E45 aids in evaluating the inclusion content within the carbon steel casting, providing an in-depth understanding of the material’s properties and performance.
“Grain size has a measurable impact on the mechanical properties of metals.”
In addition to analyzing grain size and inclusions, phase distribution is another critical parameter in determining the metal’s suitability for specific applications. Methods such as optical microscopy and X-ray diffraction enable metallurgists to examine phase distribution and discern the distinct phases within the sample, informing decisions on casting quality and material performance.
Identifying Inclusions and Segregation to Determine Metal Quality
Identifying inclusions and segregation during the metallurgical analysis of carbon steel casting is vital for ensuring metal quality assurance. Techniques like ASTM A561 for macroetching and E340 for microetching play a significant role in detecting these imperfections, which can adversely affect the casting’s reliability and performance.
Technique | ASTM Standard | Application |
---|---|---|
Macroetching | ASTM A561 | Detecting inclusions, segregations, and structural defects |
Microetching | ASTM E340 | Studying grain boundaries, phase distribution, and microstructure |
Segregation analysis is a crucial aspect of metal quality assurance, as it helps detect non-uniform distribution of alloying elements in carbon steel casting. By employing techniques such as Electron Probe Microanalysis (EPMA) and Energy Dispersive Spectroscopy (EDS), metallurgists can identify and analyze segregation, allowing for necessary modifications to the casting process to enhance the final material’s quality.
- Microstructure examination
- Grain size assessment
- Phase distribution analysis
- Identifying inclusions
- Segregation analysis
Taking all these factors into account, a thorough microstructure examination is indispensable in determining carbon steel casting quality and assuring that the material meets stringent industry standards across various applications.
Chemical Composition Analysis for Carbon Steel Alloys
As part of the metallurgical testing process, chemical composition analysis plays a vital role in determining the specific elements and compounds present in carbon steel alloys. By conducting these analyses, manufacturers can ensure that their products meet the required carbon steel alloy specifications for various applications in industries ranging from automotive to construction.
Chemical composition analysis is a crucial step in ensuring the reliability and performance of carbon steel alloy products.
Two common techniques used for chemical composition analysis of carbon steel alloys include:
- Inductively Coupled Plasma Atomic Emission Spectroscopy (ICP-AES)
- Arc Spark Spectroscopy (OES)
These state-of-the-art techniques provide precise measurements of the individual elements and compounds present in carbon steel alloys, ensuring the final product adheres to specific industry standards and maintains desired properties.
ICP-AES | OES |
---|---|
Offers rapid elemental analysis with detection limits down to parts per billion (ppb) levels. | Provides accurate trace element analysis for concentrations ranging from low parts per million (ppm) to percentage levels. |
Utilizes ionized argon gas to create plasma, which is conducive to elemental analysis. | Employs a powerful spark to generate a microplasma, facilitating a quick and robust elemental analysis. |
Widely used to investigate trace elements in liquid samples. | Commonly applied to analyze solid metallic specimens. |
In conclusion, chemical composition analysis is an integral aspect of carbon steel alloy production and metallurgical testing. Accurate results from these analyses ensure that carbon steel products meet stringent industry specifications and function optimally in a vast array of applications. Regularly performing these tests and upholding high-quality standards contribute significantly to maintaining the performance and integrity of carbon steel products in the marketplace.
Quality Control in Carbon Steel Casting with KT-Foundry
At KT-Foundry, we take quality control in carbon steel casting seriously, ensuring that all our products adhere to strict manufacturing specifications. In this section, we delve into the methods and processes we use to maintain KT-Foundry quality assurance in the production of carbon steel castings.
Ensuring Compliance with Manufacturing Specifications
Compliance with manufacturing specifications is at the core of our carbon steel casting processes. Utilizing established industry standards, we perform a range of tests on our products to measure the tensile strength, Charpy impact resistance, and chemical composition.
A vital aspect of ensuring compliance is the regular examination of our carbon steel casting standards, staying up-to-date with industry advancements and updates in testing protocols.
KT-Foundry quality control ensures that all castings are in line with industry standards, promising uncompromised quality and integrity.
Implementing Rigorous Testing Standards
At KT-Foundry, we implement rigorous testing standards in our carbon steel casting processes. Employing the latest ASTM and SAE testing methods, we can confidently assert that the carbon steel castings we produce are of the highest quality.
We utilize various tests, including:
- ASTM A370 for tensile strength tests
- ASTM E18 for hardness tests
Test Method | ASTM/SAE Designation | Purpose |
---|---|---|
Tensile strength | ASTM A370 | Evaluates the ability of the material to withstand a stretching force until it breaks or deforms |
Hardness | ASTM E18 | Measures the resistance of the material to indentation or permanent deformation |
By implementing these stringent testing standards, we can assure our customers that KT-Foundry’s carbon steel castings meet or exceed the most demanding industry specifications.
Advanced Metallurgical Testing Methods Utilized by KT-Foundry
At KT-Foundry, our commitment to producing high-quality carbon steel castings is evident in the advanced metallurgical testing methods we employ to optimize our processes. With a focus on analyzing the intricate details of the metal’s microstructures, we implement state-of-the-art techniques such as scanning electron microscopy with energy-dispersive X-ray spectroscopy (SEM/EDS) along with microhardness testing using Knoop and Vickers methods. These advanced techniques aid in refining steel casting techniques by allowing us to delve deep into the various aspects of the metal’s properties.
One of the main advantages of utilizing SEM/EDS technology lies in its ability to provide high-resolution imaging and precise elemental analysis, facilitating accurate assessments of both surface and structural characteristics. This invaluable information is then employed to fine-tune our casting processes and enhance the quality of our carbon steel products.
Scanning electron microscopy with energy-dispersive X-ray spectroscopy (SEM/EDS) offers high-resolution imaging and precise elemental analysis, helping us optimize our processes and improve product quality.
Microhardness testing methods, such as Knoop and Vickers, play a vital role in determining the hardness of metals on a microscopic scale. By examining the indentation size made by diamond surfaces under different loads, we can accurately correlate the hardness of the tested materials. As a result, these test results contribute to the development of process optimization strategies, which aim to enhance the performance of our steel castings.
- Scanning Electron Microscopy (SEM): High-resolution imaging of surfaces and structures
- Energy-Dispersive X-ray Spectroscopy (EDS): Accurate elemental analysis of the tested materials
- Knoop Microhardness Testing: Hardness measurement through the impressions made by fixed load
- Vickers Microhardness Testing: Analysis of indentation size using a diamond pyramid indenter under varying loads
Advanced Metallurgical Testing Method | Primary Purpose |
---|---|
Scanning Electron Microscopy (SEM) | High-resolution imaging of surfaces and structures |
Energy-Dispersive X-ray Spectroscopy (EDS) | Accurate elemental analysis of tested materials |
Knoop Microhardness Testing | Hardness measurement through impressions made under fixed load |
Vickers Microhardness Testing | Analysis of indentation size using a diamond pyramid indenter under varying loads |
In conclusion, the continuous implementation of advanced metallurgical testing methods at KT-Foundry is a testament to our determination and expertise in refining steel casting techniques and maintaining the highest quality standards. By embracing these technologies, we offer our customers the reliability and performance they expect from our carbon steel castings.
Interpreting the Results of Metallurgical Analysis
At KT-Foundry, interpreting metallurgical analysis involves correlating microstructure findings to casting properties. These correlations are essential for determining the suitability of various carbon steel castings and their overall quality. This section delves into the process of interpreting these results and relating them to casting properties to gain meaningful insights into the quality of materials.

Relating Microstructure Findings to Casting Properties
Microstructure analysis uncovers crucial information about carbon steel castings, including grain size, inclusion content, and phase distribution. By relating these aspects to casting properties, we at KT-Foundry can gain valuable insights into the material’s mechanical behavior and performance expectations. The table below presents an overview of typical microstructure findings and their associated casting properties.
Microstructure Finding | Associated Casting Property |
---|---|
Grain Size | Impacts yield strength, tensile strength, and ductility |
Inclusion Content | Influences fatigue resistance, corrosion properties, and fracture toughness |
Phase Distribution | Affects hardness, wear resistance, and thermal properties |
By accurately interpreting results from metallurgical analysis and relating them to casting properties, KT-Foundry can maintain its reputation for producing high-quality carbon steel castings and meeting industry demands.
“The interpretation of metallurgical analysis necessitates precision, attention to detail, and a deep understanding of microstructure correlation. At KT-Foundry, we aim to achieve that level of excellence.”
In conclusion, the interpretation of metallurgical analysis plays an integral role in understanding carbon steel casting’s mechanical behavior and performance expectations. KT-Foundry excels in this domain by correlating microstructure findings to casting properties effectively, ultimately ensuring the production of high-quality carbon steel castings for various industries.
Metallurgical Failures in Carbon Steel Casting: Prevention and Analysis
Metallurgical failures in carbon steel casting can have significant consequences for the manufacturing and end-user sectors. Understanding the underlying causes of these failures is crucial for metallurgical failures prevention and implementing foundry process improvements. Comprehensive carbon steel casting analysis plays a vital role in achieving this understanding, leading to the development of better controls and procedures.
At KT-Foundry, our team of experts conduct detailed assessments of carbon steel castings to identify defects, ascertain their causative factors, and formulate strategies to mitigate the risks associated with these failures. To enhance our efforts in error detection and prevention, we focus on:
- Materials Selection
- Mold and Gating System Design
- Refining and Heat Treatment Improvements
- Process Monitoring and Control
- Regular Testing and Analysis
One of the key procedures employed in the KT-Foundry process is plasma refining, which contributes substantially to improving the castings’ overall quality. Additionally, heat treatment modifications help ensure the final product meets the required mechanical properties and industry standards for various applications.
Typical Metallurgical Failures in Carbon Steel Casting
Carbon steel casting failures can manifest in several forms, each with its unique set of challenges and solutions. Some of the commonly observed issues include:
- Hot tearing and cracking
- Shrinkage and porosity issues
- Segregation and inclusions
- Surface defects and dimensional inaccuracies
- Improper grain structure
- Measurable mechanical property deviations
Expert analysis of these defects is crucial for understanding their origin, devising appropriate countermeasures, and optimizing foundry processes to achieve better casting outcomes.
“A well-conducted metallurgical analysis not only helps identify carbon steel casting failures, but also presents opportunities to enhance manufacturing techniques and prevent future defects.”
Reducing Metallurgical Failures through Continuous Improvement
Success in reducing metallurgical failures in carbon steel casting hinges on the continuous improvement of foundry processes. By systematically analyzing defects, collecting relevant data, and comparing results with established industry benchmarks, KT-Foundry has been able to implement targeted corrective actions to minimize defect occurrence and enhance overall casting quality, thus catering to a wide range of applications and industries.
Conclusion
In summary, the importance of metallurgical analysis in carbon steel casting cannot be overstated. It involves an extensive array of techniques designed to ascertain the material’s final properties, such as grain size, inclusion content, and phase distribution. These insights help ensure the production of high-quality metals and compliance with industry standards.
With ongoing advancements in carbon steel casting and the development of rigorous testing methods, the industry continues to evolve and improve. Many of these improvements are the result of the commitment of companies like KT-Foundry, which diligently work to implement robust quality control measures, and continuously optimize their casting processes.
Through KT-Foundry’s dedication to excellence, the reliability and performance of carbon steel castings have been greatly enhanced, offering significant benefits to various industries. In essence, metallurgical analysis serves as the backbone for these advancements, providing invaluable insights and laying the groundwork for continuous improvement and refinement of carbon steel casting processes.
FAQ
What is the significance of metallurgical analysis in carbon steel casting?
Metallurgical analysis is essential for understanding the chemical, physical, and mechanical properties of carbon steel and ensuring the reliability and performance of the final casting. Through microstructure observation and various testing methods, analysts can evaluate critical factors such as grain size, inclusion content, phase distribution, and porosity that impact carbon steel’s suitability for its intended application.
How does microstructure examination support quality control in carbon steel casting?
Microstructure examination of carbon steel casting provides insights into grain size and phase distribution, which are crucial for assessing the material’s final properties and its suitability for various applications. It also helps in identifying inclusions and segregation that can impact the casting’s performance and reliability.
What methods are used for chemical composition analysis of carbon steel alloys?
Chemical composition analysis methods such as Inductively Coupled Plasma Atomic Emission Spectroscopy (ICP-AES) and Arc Spark Spectroscopy (OES) are employed to determine the specific elements and compounds present in carbon steel alloys, ensuring that the steel meets the required industry specifications for its intended use.
How does KT-Foundry maintain quality control in carbon steel casting?
KT-Foundry enforces compliance with specific manufacturing specifications and rigorously applies various testing procedures, such as tensile and charpy testing, as well as chemical analysis, to maintain quality control in carbon steel casting and to meet or exceed industry standards.
What advanced metallurgical testing methods are utilized by KT-Foundry?
KT-Foundry employs advanced metallurgical testing methods such as scanning electron microscopy with energy-dispersive X-ray spectroscopy (SEM/EDS) and microhardness testing (Knoop and Vickers) to optimize the casting process and enhance the quality of carbon steel products.
How are the results of metallurgical analysis interpreted?
Interpreting metallurgical analysis involves correlating microstructure findings, such as grain size, inclusion content, and phase distribution, to the casting properties and expectations in terms of mechanical behavior and performance.
How can metallurgical failures in carbon steel casting be prevented and analyzed?
Metallurgical failures in carbon steel casting can be prevented and analyzed through comprehensive understanding of the causes. Expert analysis helps develop stringent controls and procedures, such as plasma refining and heat treatment modifications, to minimize defect occurrence and enhance overall casting quality.