In the vast world of carbon steel casting, mechanical properties are critical components in determining the quality, integrity, and performance of the finished product. These properties, including tensile strength, impact resistance, and hardness, are all essential aspects of the casting process. Quality control is vital throughout the entire process, from design and material selections to heat treatments and surface preparations. A meticulous approach to testing is necessary to guarantee the overall quality, integrity, and durability of carbon steel castings.
Let’s begin our in-depth exploration of mechanical testing in carbon steel casting, discussing the importance of various tests and standards, and how they contribute to the final product.
Key Takeaways
- Mechanical properties are vital in determining the quality of carbon steel castings
- Quality control throughout the entire process is essential to ensure casting integrity
- Tensile strength, impact resistance, and hardness are critical aspects of mechanical testing
- Rigorous standards and test methods guide the evaluation of carbon steel casting properties
- Proper testing contributes to the overall durability and performance of the finished product
Understanding the Importance of Mechanical Testing in Carbon Casting
Mechanical testing in carbon casting plays a vital role in quality verification, ensuring that the products meet the required ASTM standards for mechanical properties. It is crucial to remember that such tests serve to verify the quality of the material and are not intended to establish the final properties of the casting. Testing methods include tensile strength, yield strength, elongation, reduction of area, and hardness, all of which are measured at room temperature. Rigorous standards and methods guide these tests to ensure the integrity and quality of carbon steel castings.
Quality verification, in the context of mechanical testing, is based on ASTM standards that utilize test coupons, which may differ from the property characteristics of the actual cast product. Test coupons are typically derived from standard keel blocks, and their properties are recognized to differ from those of the actual casting due to variables like section size and heat treatment.
Carbon steel castings play a vital role in various industries like automotive, construction, and aerospace. Ensuring their properties through mechanical testing is essential in producing safe, reliable, and high-performance components.
Through mechanical testing, we can assess the casting properties of carbon steel components, ensuring that they meet the necessary quality standards. This process is fundamental in achieving a consistent and reliable product that will perform optimally in real-world applications. The importance of mechanical testing cannot be overstated, as it directly impacts the overall performance and longevity of carbon steel castings.
- Tensile testing,
- Yield strength testing,
- Elongation measurement,
- Reduction of area evaluation,
- Hardness testing.
Comprehensive mechanical testing in carbon casting helps in minimizing potential risks associated with the final product, ensuring both the safety and performance of the components produced. By following ASTM standards, manufacturers can achieve quality verification and make informed decisions based on objective, reliable data.
As a result, mechanical testing is a critical aspect of carbon casting operations, contributing to both the development of high-quality products and the overall success of the industry.
Enhancing Quality Control in Casting with Tensile Strength Testing
For carbon steel castings, tensile strength and other mechanical properties are measured using precise testing methods and are subject to rigorous industry standards. These standards dictate specimen shape, size, surface quality, and the correct cutting, clamping, and testing rates. The tensile specimens can be derived from various locations and treatments, conforming to the GBT228 “Metallic Material Tensile Test Method at Room Temperature” requirements.
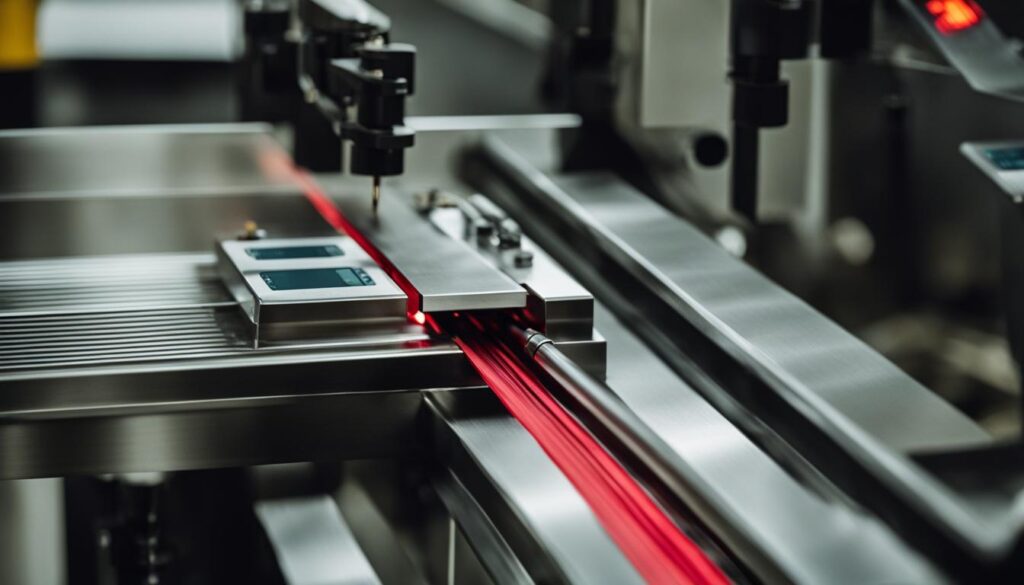
Tensile Test Procedures and Standards
The process of tensile strength testing involves pulling a specimen under a load until it reaches the point of failure. This assessment allows the determination of important mechanical properties, such as yield strength, elongation, and fracture resistance, that are vital for the integrity of carbon steel castings. Several key considerations for tensile testing include:
- Specimen selection, preparation, and designation.
- Appropriate testing equipment and precise measurement techniques.
- Proper interpretation and analysis of test data.
- Adherence to established quality control protocols.
For accurate tensile strength results, it is essential to follow prescriptive standards such as ASTM A370, ASTM E8, and ISO 6892-1. Each of these standards provides detailed guidelines for the entire tensile testing process, including specimen dimensions, loading rates, and reporting criteria.
Evaluating Tensile Strength Results for Carbon Steel Integrity
The evaluation of tensile test results includes ensuring the specimen is free of mechanical damage, cracks, and deformities. Results are based on the calculation and processing methods conforming to standard specifications. A crucial aspect of the evaluation process is comparing the obtained outcomes to the expected values, as specified in carbon steel tensile testing standards. This comparison ensures that the castings meet the required levels of carbon steel integrity.
“The meticulous evaluation of tensile test results plays a critical role in confirming the quality of carbon steel castings, ultimately ensuring they are suitable for their designated applications.”
Upon the completion of a tensile test, the final values are systematically recorded to conform to industry standards. The following table outlines some of the essential data that can be obtained during tensile testing:
Property | Description |
---|---|
Yield Strength | The stress at which a material begins to deform plastically. |
Tensile Strength | The maximum stress that a material can withstand while being stretched or pulled. |
Elongation | The percentage increase in length of a material when it is subjected to tensile stress until failure. |
Reduction of Area | The percentage decrease in the cross-sectional area of a material when it is subjected to tensile stress until failure. |
In conclusion, tensile strength testing plays a vital role in enhancing quality control in casting by adhering to strict industry standards. Furthermore, the meticulous evaluation of test results ensures that carbon steel castings meet the required levels of integrity and can successfully withstand the stresses of their intended applications.
Ensuring Durability Through Impact Testing
Impact testing plays a critical role in evaluating the durability of carbon casting materials. It measures the energy absorbed by a material during fracture under rapid loading, providing vital information on a casting’s fracture resistance. By conducting thorough impact testing, manufacturers are better equipped to detect and ultimately address potential vulnerabilities in the casting’s mechanical properties.
The Role of Impact Testing in Evaluating Fracture Resistance
Fracture resistance evaluation is an essential aspect of impact testing in carbon casting. To ensure accurate results and minimize inconsistencies, the process follows the standard GB/T229-2007 “Charpy Pendulum Impact Test Method for Metallic Materials”. This method encompasses specific requirements for the shape, dimension, and technical conditions of the test specimens, which can vary depending on the properties of the material being tested. An effective impact testing strategy helps guarantee that the final casting product has the desired fracture resistance.
“Impact testing provides crucial insights into fracture resistance and overall durability in carbon casting, promoting the development of reliable and long-lasting products.”
- Selection of appropriate test specimens according to material properties
- Adhering to standard GB/T229-2007 for specimen shape, dimension, and technical conditions
- Minimizing inconsistencies and errors in test results through strict adherence to testing procedures
- Ensuring the final carbon casting product meets or exceeds the desired level of fracture resistance
The following table highlights some key parameters associated with the Charpy Pendulum Impact Test method, providing insight into the factors considered during fracture resistance evaluation:
Parameter | Charpy Pendulum Impact Test Method |
---|---|
Standard | GB/T229-2007 |
Test Specimen Shape | Depends on the material’s properties |
Test Specimen Size | As per standard requirements |
Technical Conditions | Specific requirements outlined in the standard |
In conclusion, impact testing is a fundamental aspect of ensuring durability in carbon casting by evaluating the material’s fracture resistance capabilities. By following specific guidelines and industry standards, our impact testing methods contribute to producing reliable, high-quality carbon steel castings known for their resilience.
Hardness Testing: A Critical Factor in Cast Carbon Steel Performance
Hardness testing plays a vital role in determining the resistance of cast carbon steel to deformation and ultimately, in evaluating its performance. Two commonly used methods in this process are the Brinell Hardness Method and the Rockwell Hardness Method. The selection of an appropriate method depends on the metallographic structure and is governed by specific industry standards.
The Brinell Hardness Method is outlined in GBT231.1-2002 “Metal Brinell Hardness Part I: Test Method“, while the Rockwell Hardness Method adheres to the guidelines specified in GB/T 230.1-2004 “Metal Rockwell Hardness Part 1: Test Method“.
Hardness testing methods such as Brinell and Rockwell contribute significantly to ensuring optimal cast carbon steel performance by assessing resistance to deformation.
These hardness testing methods possess individual characteristics that cater to specific applications and requirements. Below is a comparative analysis of the two methods:
Hardness Method | Key Advantages | Limitations |
---|---|---|
Brinell Hardness Method | Applicable to a wide range of materials, including softer metals.Provides deep indentation, allowing for accurate results. | Manual interpretation of results required.Less suitable for thin or hardened surfaces. |
Rockwell Hardness Method | Rapid measurement and results interpretation.Scalable across a wide range of hardness values. | Not suitable for brittle materials or irregular surfaces.Indentation is relatively shallow, which might result in less accurate results. |
Selecting the appropriate hardness testing method and adhering to industry standards ensures that cast carbon steel components exhibit resistance to deformation and consistently deliver optimal performance.
Comprehensive Testing for Reliable Carbon Steel Castings at KT-Foundry
At KT-Foundry, we are committed to providing top-quality carbon steel castings through comprehensive and advanced testing methods. Our approach ensures the hardiness and reliability of our products by evaluating critical mechanical properties, including hardness, tensile strength, and impact resistance, among others.
Our Approach to Certifying Steel Casting Hardiness
We recognize the importance of Steel Casting Hardiness Certification in delivering superior products to our clients. Our comprehensive testing process involves:
- Adhering to industry-standard techniques for mechanical testing
- Ensuring castings meet all required specifications and standards
- Continuously updating our testing methods and equipment
- Maintaining strict quality control measures throughout the entire production process
Our rigorous approach to testing guarantees that our customers receive reliable steel castings that meet the highest standards of quality, performance, and durability.
Developing Advanced Casting with Optimal Mechanical Properties
We don’t just focus on certifying the hardiness of our products; we also prioritize refining our casting designs to achieve optimal mechanical properties through:
- Choosing appropriate materials for each project
- Utilizing the latest technological advancements in carbon steel casting
- Applying suitable heat treatments and post-production processes
- Working closely with clients to optimize casting geometry and section size
By continually refining our KT-Foundry Casting Design processes, we ensure that each product we deliver possesses the perfect combination of mechanical properties to meet our clients’ unique performance requirements.
Aspect | Focus |
---|---|
Materials selection | Choosing the right alloys and materials to meet project specifications |
Design optimization | Customizing casting geometry and section size to fulfill performance requirements |
Heat treatments | Applying strategic thermal processes to achieve desired hardiness and durability |
Quality control | Maintaining strict inspection and quality assurance throughout the casting process |
In conclusion, our commitment to comprehensive testing, Advanced Carbon Steel Casting, and collaboration with clients allows KT-Foundry to consistently deliver reliable castings that exhibit optimal mechanical properties. As a result, our customers can trust us to provide premium products that stand the test of time.
Case Studies: Demonstrating Excellence in Carbon Steel Casting Tests
Our commitment to excellence in carbon steel casting tests is further proven through various Carbon Steel Casting Case Studies. We have chosen a select few examples that showcase how our casting processes, material selection, and design considerations have led to components that exceed industry standards for strength, ductility, and performance.
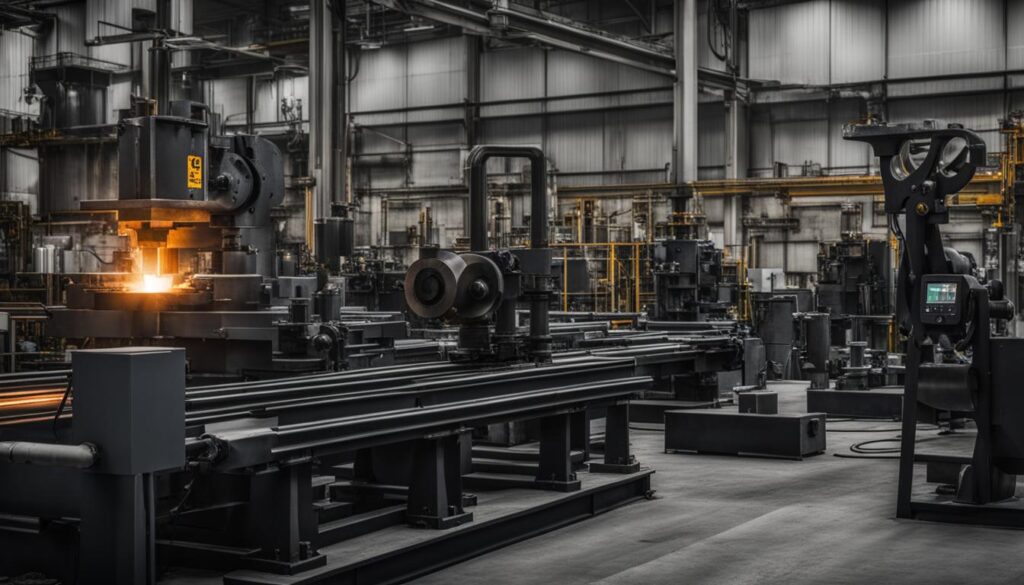
In one case study, we worked with an automotive manufacturer to improve the performance and durability of a key engine component. The original design featured a carbon steel casting with suboptimal properties, leading to premature wear and potential failure under extended use.
Through a thorough KT-Foundry Results Analysis, we identified weaknesses in the casting design and were able to recommend changes that would significantly enhance the mechanical properties of the component.
These changes included:
- Optimizing the geometry of the casting for improved stress distribution
- Selecting a more appropriate carbon steel grade with higher tensile strength and ductility
- Implementing advanced heat treatment processes to maximize the durability of the casting
After implementing our recommendations, the revised component exceeded the industry benchmarks for tensile strength, elongation, and impact resistance, ensuring a longer service life and better performance. This successful collaboration is a testament to our Testing Excellence and ability to deliver reliable, high-performance carbon steel castings.
Another case study features our work with a heavy machinery company that required a wear-resistant carbon steel casting for a large industrial machine. The original component exhibited inadequate wear resistance and low impact toughness, leading to frequent replacements and costly downtime.
Our KT-Foundry Results Analysis uncovered opportunities for improvements in the casting’s material composition and heat treatment procedures, leading to a significant enhancement of the required mechanical properties.
These improvements included:
- Utilizing a higher-grade carbon steel with enhanced wear resistance and impact toughness
- Refining heat treatment processes for optimized hardness and toughness balance
- Collaborating with the client on an updated design for better performance in demanding industrial applications
The newly developed component showcased outstanding mechanical properties, far surpassing industry standards. This success story highlights our expertise in delivering carbon steel castings with optimal mechanical properties.
In conclusion, these case studies serve to demonstrate our dedication to producing exceptional carbon steel castings through thorough evaluation and testing. Our ability to analyze and optimize the manufacturing process allows us to guarantee that our clients receive components that consistently meet and surpass industry expectations for performance and durability.
Conclusion
At KT-Foundry, we take pride in our commitment to producing reliable carbon steel castings through superior casting processes. Our stringent approach to mechanical testing and quality control is designed to deliver castings that consistently meet or exceed industry standards.
By leveraging advanced technology and industry best practices, we are able to achieve superior casting processes that ensure the integrity, durability, and performance of our products. Our team of experts takes great care to address every aspect of the casting process, from material selection and design considerations to rigorous testing and final analysis.
In the final analysis, the dedication and expertise we bring to our work at KT-Foundry ensure our clients receive carbon steel castings of the highest quality. By prioritizing testing and quality control, we confidently provide products that meet the specific needs of our customers and excel under demanding conditions.
FAQ
What are the key mechanical properties measured in carbon steel casting tests?
The key mechanical properties tested in carbon steel casting include tensile strength, yield strength, elongation after fracture, reduction of area, deflection, impact absorption, and hardness. These tests are conducted to ensure the quality and integrity of carbon steel castings.
How do ASTM standards contribute to mechanical testing in carbon steel casting?
ASTM standards provide guidelines for test coupon specimens to be used in the verification of material quality in carbon steel casting. The standards ensure precise and accurate measurements in tensile strength and other mechanical tests based on test coupon properties that may differ from the finished casting.
What are some of the industry-standard tensile strength testing practices?
Tensile strength tests are conducted based on standard procedures that dictate specimen shape, size, surface quality, and proper cutting, clamping, and testing rates. These specimens are derived from different locations and treatments and must conform to GBT228-2014 “Metallic Material Tensile Test Method at Room Temperature” requirements.
Why is impact testing vital in the carbon steel casting process?
Impact testing measures the energy absorbed by a material during fracture under rapid loading. It helps determine a casting’s fracture resistance, which is crucial for evaluating its durability and overall performance. The standard followed for this test is GB/T229-2007 “Charpy Pendulum Impact Test Method for Metallic Materials”.
What are some common hardness testing methods used in carbon steel casting?
Hardness testing methods include Brinell and Rockwell tests. These methods measure the resistance of carbon steel castings to deformation. The chosen test method is based on the metallographic structure, and specific instruments and procedures are outlined in GBT231.1-2002 “Metal Brinell Hardness Part I: Test Method” and GB/T 230.1-2004 “Metal Rockwell Hardness Part 1: Test Method”.
What sets KT-Foundry apart in terms of carbon steel casting testing and quality control?
KT-Foundry adopts advanced, comprehensive testing methods to ensure the durability and reliability of carbon steel castings. By following rigorous industry-standard techniques for mechanical testing, we ensure that our castings meet required specifications and standards. We also collaborate with clients to optimize casting geometry and section size for optimal mechanical and performance requirements.
How do case studies demonstrate the excellence of KT-Foundry’s carbon steel casting tests?
Case studies showcase the casting processes, material selection, and design considerations employed by KT-Foundry. They illustrate how these practices lead to components that exceed industry standards for strength, ductility, and performance, highlighting our commitment to producing high-quality carbon steel castings.