In the world of carbon steel casting, maintaining the integrity and quality of the final product is of utmost importance. With the aid of advanced technologies and methodologies, we can effectively identify and rectify defects in carbon steel castings, ensuring the highest possible level of quality and performance. Through the implementation of automated and manual defect detection methods, such as computer vision and AI, we are able to uncover inconsistencies and flaws that could compromise the casting’s overall effectiveness. Once these defects have been pinpointed, a strategic rectification process is enacted, combining cutting-edge metal arc welding techniques and inclusion analysis to repair the casting and optimize its quality. Such an approach not only guarantees that our carbon steel castings meet predefined standards and specifications but also contributes to the long-term sustainability of manufacturing processes by ensuring a proactive approach to defect prevention and resource optimization.
Key Takeaways
- Effective defect detection and rectification safeguards the integrity and quality of carbon steel castings.
- Advanced technologies such as computer vision and AI enhance the precision of defect identification.
- Rectification processes involve metal arc welding techniques and thorough analysis of inclusion characteristics.
- Efficient defect management leads to optimized quality, reduced waste, and improved sustainability of manufacturing processes.
- Industry advancements pave the way for innovative detection methods and ongoing improvements in the field of carbon steel casting.
The Importance of Quality Control in Casting Processes
Effective quality control is paramount in casting processes to ensure the final product meets industry standards and safety requirements. Defects in carbon steel castings, such as porosity or inclusions, can compromise product integrity and lead to potential safety hazards. The implementation of standards and proprietary specifications, such as those from ASTM and ISO, is crucial for defining acceptable chemical compositions and mechanical properties, which influence the functional robustness of the casting.
Understanding the Impact of Defects on Product Integrity
Methods like KT-Foundry’s approach involve visual inspections for surface discontinuities and adherence to nationally recognized specifications and codes to prevent defects that hinder structural and mechanical integrity. Detecting and rectifying casting defects not only improve overall product quality but also minimize costly failures and consequent financial losses.
Advancements in Porosity Detection Techniques
The industry’s commitment to innovation has led to substantial advancements in porosity detection techniques. These advancements have improved the precision and speed of detecting defects within the castings, thereby enhancing the overall quality control process. Advanced porosity detection leverages technologies such as computerized tomography and ultrasonic testing, allowing for non-destructive ways to identify internal voids and gas pockets that could weaken the casting.
Adherence to stringent control measures and utilizing state-of-the-art detection methods ensure high-quality castings and reduce the risk of failure upon deployment in critical applications.
KT-Foundry’s Approach to Ensuring Casting Excellence
KT-Foundry advocates a systematic approach to ensuring casting excellence through the incorporation of rigorous quality control measures and continuous process evaluation. The foundry employs advanced inspection techniques, including digital radiography and magnetic particle inspections, to identify defects early in the manufacturing process. Additionally, KT-Foundry has developed proprietary processes that standardize the handling and treatment of castings, resulting in a consistent product that matches or exceeds industry expectations.
Defect Detection Method | Benefits |
---|---|
Visual Inspection | Cost-effective, detects surface discontinuities |
Digital Radiography | High-resolution imaging, non-destructive, reveals internal defects |
Magnetic Particle Inspection | Identifies surface-breaking discontinuities in ferrous materials |
Ultrasonic Testing | Highly sensitive, non-destructive, detects both surface and subsurface defects |
Computerized Tomography | Comprehensive visualization, identifies internal voids and gas pockets |
These processes entail meticulous documentation and adherence to performance criteria, ensuring a relentless pursuit of excellence in carbon steel casting manufacturing.
Innovative Methods for Inclusion Analysis in Carbon Steel
Carbon steel casting is continually evolving, with the industry striving to enhance the reliability of cast products. One of the main focuses is finding innovative ways to conduct inclusion analysis, which helps to identify and characterize non-metallic materials within the casting that could potentially compromise mechanical properties and end-use performance. Inclusion analysis, when executed using cutting-edge examination methods, provides valuable insights that enable foundries to refine their manufacturing processes, reduce the occurrence of detrimental inclusions, and deliver castings with superior mechanical characteristics and durability.
Scanning electron microscopy and energy dispersive X-ray spectroscopy are employed to analyze inclusions at a microstructural level, providing insight into the origin, type, and distribution of inclusions.
Notably, the data gathered from SEM and EDS analyses have proven invaluable for casting inclusion analysis. Below is an overview of the key output parameters of these innovative examination methods:
- Inclusion composition and origin
- Inclusion size, shape, and distribution
- Inclusion density and population
- Correlation between inclusions and mechanical properties
Obtaining such data enables foundries to directly target the root causes of inclusions and implement changes that will ultimately improve the performance of carbon steel castings. By employing these advanced analytical techniques, manufacturers can more efficiently address any defects that may arise, thereby ensuring the highest possible quality for their products.
The following table provides a summary of the primary benefits of implementing these innovative examination methods for inclusion analysis:
Examination Method | Advantages |
---|---|
Scanning Electron Microscopy | Superior image resolution and magnification, detailed morphological examination, flexibility in sample orientation |
Energy Dispersive X-ray Spectroscopy | Rapid elemental analysis, non-destructive method, precise and accurate compositional data |
In conclusion, innovative methods for inclusion analysis, such as SEM and EDS, are essential to the ongoing refinement of carbon steel casting processes. By employing these advanced techniques, foundries can gain valuable insights into the characteristics of non-metallic materials within their products, allowing for continuous improvement in casting quality and performance. As a result, the industry can deliver carbon steel castings with consistently high levels of mechanical strength and durability, fulfilling their customers’ expectations and requirements.
Strategies for Effective Weld Repair in Carbon Steel Castings
When defects occur in carbon steel castings, effective weld repair strategies that align with sustainability objectives become crucial in restoring their integrity. By implementing best weld repair practices, foundries can account for various factors, such as the extent of repair, relative cost, and environmental impact. By focusing on environmentally responsible repair techniques, manufacturers can minimize additional material usage, conserve resources, and extend service life.
Optimizing Repair Procedures for Improved Sustainability
Sustainable repair techniques include post-heating operations, the choice of compatible electrodes, and meticulous preparation of welding surfaces. Implementing these practices results in reduced environmental impact and the creation of castings with a longer service life.
Automated versus Manual Welding: Benefits and Drawbacks
The debate between automated and manual welding in the steel casting repair context presents various factors to consider when choosing the most appropriate method. While automated welding offers consistency, repeatability, and efficiency, it may lack adaptability and skilled craftsmanship in specific situations. Conversely, manual welding provides the benefit of greater flexibility and expert judgment from experienced welders, particularly useful in custom or complex repair scenarios. However, the drawback of manual welding is its time-consuming nature and potential variability in repair quality due to the varying skill levels of individual welders.
Implementing Durable Solutions for Long-Term Performance
Implementing durable weld repair solutions is essential to ensuring the carbon steel castings’ long-term performance. These repair methods address immediate defects while considering the long-term implications of the repair on casting performance under expected service conditions. Selecting appropriate welding consumables and applying stringent post-weld heat treatments contribute to a repair that is both structurally sound and capable of withstanding future operational stresses.
Our primary goal is to restore the carbon steel casting to its original specifications or better, safeguarding its longevity and functionality in its intended application.
Repair Method | Advantages | Disadvantages |
---|---|---|
Automated Welding | Consistency, repeatability, efficiency | Limited adaptability, unsuitable for custom repairs |
Manual Welding | Flexibility, expert judgment | Time-consuming, variability in repair quality |
In conclusion, by adopting effective weld repair strategies and balancing the benefits and drawbacks of both automated and manual welding techniques, foundries can successfully repair carbon steel castings, ensuring long-term performance and sustainability in the process.
Computer Vision and AI in Automated Defect Detection
The integration of computer vision and AI in automated defect detection represents a transformative shift in quality control for carbon steel castings. These technologies enable rapid and accurate detection of surface and subsurface defects by analyzing visual data through sophisticated algorithms. Computer vision in casting and AI defect detection systems learn from collected data to improve their detection accuracy over time and can handle complex inspection tasks with minimal human intervention.
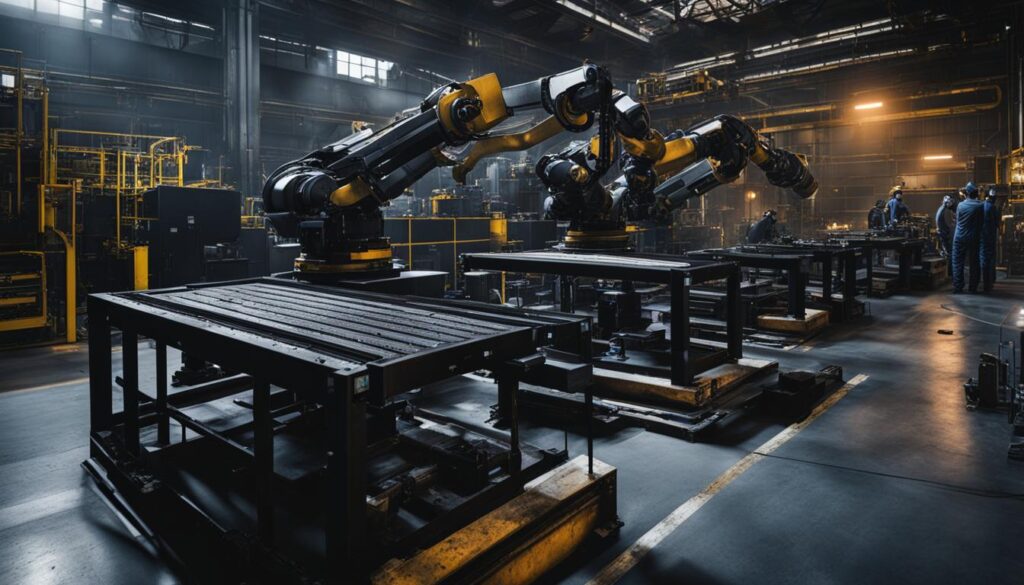
By automating inspection processes, foundries reap the benefits of enhanced reliability and quality in their casting products. Furthermore, the time and cost associated with manual inspections are substantially reduced. Let’s explore some essential aspects of computer vision and AI in defect detection:
- Advanced image processing techniques
- Increased accuracy and efficiency
- Adaptability to different casting types and defect categories
- Reduced reliance on manual inspections
Incorporating computer vision and AI-driven defect detection systems in the casting industry accelerates the identification and rectification of defects, leading to a higher degree of overall product quality and customer satisfaction.
Spearheading these advancements, automated inspection technology paves the way for a future where precision and efficiency in the casting industry become the norm. By embracing and refining these innovative technologies, foundries can distinguish themselves as industry leaders committed to providing carbon steel casting products of exceptional quality and structural integrity.
Environmental and Economic Benefits of Precision Casting
Precision casting techniques have significant environmental and economic advantages, chief among them the potential for reducing carbon emissions. Innovations in manufacturing processes, such as the adoption of lean energy-saving models and the integration of new materials with lower carbon footprints, contribute to this reduction. By minimizing waste and optimizing resource use, these advanced techniques not only reduce environmental impact but also enhance efficiency and cost-effectiveness of the production process, benefiting both the planet and the bottom line.
Reducing Carbon Emissions Through Advanced Manufacturing Techniques
Advanced manufacturing techniques contribute to the carbon emissions reduction in the casting industry. For instance, the implementation of resource optimization strategies enables foundries to improve energy consumption, lower waste generation, and minimize the raw material required in production. This leads to a decrease in greenhouse gas emissions and positions the casting industry as an eco-friendly and sustainable sector. Moreover, utilizing cutting-edge technologies for the production process further bolsters green manufacturing efforts.
How Intelligent Manufacturing Aids in Resource Optimization
Intelligent manufacturing systems leverage advanced data analytics, machine learning, and automation to streamline and optimize resource usage while improving manufacturing processes. These smart production processes provide real-time analysis and feedback, allowing for more precise control over casting processes and reducing material waste. In addition to lowering operational costs, intelligent manufacturing contributes to energy conservation by automating process adjustments for optimized energy consumption. This results in more sustainable production practices and a decrease in resource utilization, bolstering the industry’s commitment to a greener future.
Minimizing Financial Strain with Efficient Defect Management
Efficient defect management is crucial for minimizing financial strain within the manufacturing industry. By implementing robust detection, repair, and prevention strategies, foundries can significantly reduce costs associated with scrap and rework while minimizing waste generation. Effective defect management goes beyond rectification, incorporating predictive analytics and zero-defect manufacturing concepts to address potential issues before they occur.
Efficient defect management ensures that resources are allocated efficiently, production cycles are optimized, and economic losses linked to defects and inefficiencies are mitigated.
- Precise defect detection technologies for early identification
- A well-structured rectification process to repair the casting
- Continuous improvement efforts for defect prevention
Precision casting, advanced manufacturing techniques, and intelligent manufacturing systems pave the way for a more eco-friendly and cost-effective approach to producing high-quality castings. By embracing these technologies and practices, the industry moves closer to achieving sustainable growth while delivering exceptional products to customers all over the world.
Conclusion
In the pursuit of excellence and sustainability within the carbon steel casting industry, defect detection and rectification remain crucial elements. Embracing technological advancements, such as computer vision, AI, and intelligent manufacturing, combined with stringent quality control standards and innovative repair techniques, allows the industry to overcome challenges arising from defects. As a result, there is an optimized production process that offers environmental benefits, economic advantages, and a commitment to continuous improvement in carbon steel casting.
By following industry best practices and utilizing cutting-edge detection methods, foundries can improve casting process efficiency, reduce waste and energy consumption, and enhance the reliability of their products. This not only benefits the bottom line but also demonstrates a dedication to delivering high-quality, dependable carbon steel castings to the market.
It is essential to maintain a relentless pursuit of improvement in carbon steel casting processes and defect management, thereby ensuring a streamlined production cycle, minimization of financial strains, and adherence to strict industry standards and specifications. Through consistent dedication to excellence and a proactive approach to defect mitigation, the carbon steel casting industry can continue to prosper, producing the finest products that meet the highest expectations.
FAQ
What is the impact of defects on carbon steel castings?
Defects in carbon steel castings can significantly impact their structural and functional integrity, leading to reduced efficacy and potential failure in application. This underlines the importance of quality control in casting processes to ensure the final product meets industry standards and safety requirements.
What advancements have been made in porosity detection techniques?
Advancements in porosity detection techniques, such as computerized tomography and ultrasonic testing, have improved the precision and speed of detecting defects within castings, thereby enhancing the overall quality control process and ensuring high-quality products with reduced risk of failure.
How does KT-Foundry approach ensuring casting excellence?
KT-Foundry employs advanced inspection techniques, including digital radiography and magnetic particle inspections, to identify defects early in the manufacturing process. They also utilize proprietary processes that standardize the handling and treatment of castings, resulting in a consistent product that matches or exceeds industry expectations.
What are some innovative methods for inclusion analysis in carbon steel castings?
Techniques such as scanning electron microscopy and energy dispersive X-ray spectroscopy are employed to analyze inclusions at a microstructural level, providing insight into the origin, type, and distribution of inclusions. This enables foundries to refine their manufacturing processes, reduce the occurrence of detrimental inclusions, and ultimately deliver castings with superior mechanical characteristics and durability.
What are the key considerations for effective weld repair in carbon steel castings?
Effective weld repair strategies should take into account factors like the extent of repair, relative cost, and environmental impact. Techniques such as post-heating operations, choice of compatible electrodes, and meticulous preparation for welding surfaces are crucial components of a sustainable repair protocol.
How do computer vision and AI contribute to automated defect detection?
Computer vision and AI enable rapid and accurate detection of surface and subsurface defects by analyzing visual data through sophisticated algorithms. AI-driven defect detection systems learn from collected data to improve their detection accuracy over time, reducing the time and cost associated with manual inspections.
How can precision casting techniques benefit the environment and economy?
Precision casting techniques can reduce carbon emissions through the adoption of lean energy-saving models, new materials with lower carbon footprints, and optimization of resource use. This minimizes waste and boosts efficiency, resulting in both environmental and economic benefits.
What are the advantages of intelligent manufacturing systems in the casting industry?
Intelligent manufacturing systems leverage advanced data analytics, machine learning, and automation to optimize resource usage, improve manufacturing processes, reduce material waste, and conserve energy. This leads to more sustainable production practices and lower operational costs.
How does efficient defect management minimize financial strain in the manufacturing industry?
By implementing robust detection, repair, and prevention strategies, foundries can significantly reduce the costs associated with scrap and rework. Proactive approaches, such as predictive analytics and zero-defect manufacturing concepts, help anticipate potential issues before they occur, ensuring efficient resource allocation and optimized production cycles.