One of the oldest and most common types of casting is sand casting, usually done by iron foundries. It is a more popular choice than other metal manufacturing processes because of its simple production process and lower production costs.
It is the primary choice among all casting processes, especially those who need to produce large quantities of metal parts on a tight budget. However, like other metal castings, it also has its own advantages and disadvantages.
Creating The Sand Mold
Although the process can be quite complex, it’s not difficult to create a sand mold. For every sand mold you create, you’ll need to have a pattern. This is basically a model of the object you want to make. You can either carve the pattern out of wood or 3D print it.
Once you have your pattern and sand, it’s time to start creating the mold. Begin by packing the sand into the pattern, making sure to pack it tightly. Then, remove the pattern and use a trowel to smooth the surface of the sand.
The next step is to prepare the molten metal. The produced metal casting can then be further machined and finished as needed.
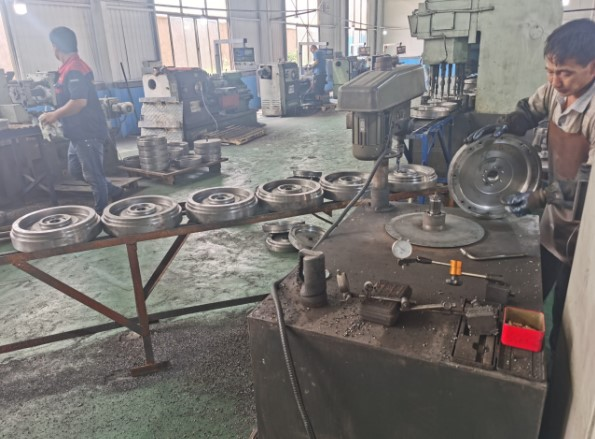
Green Sand Casting Process
The green sand casting process is similar to the regular sand casting process. The green sand mold is made from very fine green sand and a binder, created in a flask.
This flask is then placed in a special furnace in an iron foundry, where it undergoes heat treatment under a specific temperature so that the sand holds its shape.
After the sand has been heated, the molten material is poured into the flask.
It is more affordable compared to resin sand castings. Green sand castings are the better choice for projects, especially since iron prices continue to rise.
Advantages of Sand Casting
The process has many advantages, making it an attractive option for metal part production.
Low-Cost
Sand casting is an economical way to manufacture parts because the raw materials are readily available and relatively inexpensive. The process itself is also relatively simple and does not require specialized machinery or tools.
In addition, sand molds can be reused. It reduces the cost of production and allows the iron foundries to pass the savings on to their customers.
Versatile
Compared to die casting, this process is highly customizable, allowing for intricate details and precision parts. This makes sand casting an ideal choice for complex parts with tight tolerances.
This process can be used for the creation of parts and components that have specific properties such as wear resistance or heat resistance.
Ability to Produce Castings Quickly
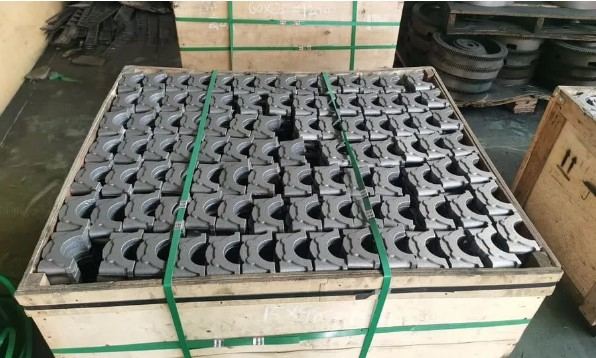
Sand castings can be produced in large quantities more quickly and efficiently than other manufacturing processes.
Since it does not require complex machinery or a lot of preparation, it is an ideal choice for projects that require a quick turnaround.
Since the sand can be reused multiple times, it is possible to produce parts in a shorter time frame than with other processes. The sand casting process is ideal to produce castings for time-sensitive projects.
Disadvantages of Sand Casting
Its many advantages come with drawbacks. Though these can be avoided or can be corrected, it is still important to know the possible disadvantages of sand casting.
Prone to Surface Defects
The sand mold is not as precise as other methods, which can lead to lower dimensional accuracy.
Sand has tiny air pockets that can trap gas bubbles during the casting process, which can lead to sand holes affecting the casting quality.
However, these defects can be addressed by using finer sands, using a higher pressure when pouring the molten metal, reducing the pouring temperature, and using a vacuum to remove any trapped gas bubbles.
Additionally, manufacturers can use coatings and surface treatments to reduce the risk of metal defects.
Rough Surface Quality
The roughness of the surface is due to two primary factors. The sand particles on the surface of the mold become fused to the metal, which creates a rough surface.
Secondly, parts often contain porosity, or tiny air bubbles, which further contribute to the roughness.
In some cases, the rough surface of parts can be beneficial. For example, if the part will be used in a high-friction application, the rough surface can provide additional grip.
For these reasons, it is important to consider the potential disadvantages of this casting process before selecting it. While it can be a cost-effective and reliable process, the rough surface of the cast parts can be a significant limitation.