As the economy continues to evolve, businesses of all sizes are increasingly turning to the foundry industry to produce metal castings they need to stay competitive. Foundries offer a wide range of benefits, from cost savings to improved production times, that make them an attractive option for businesses looking to increase their efficiency and productivity.
When it comes to manufacturing metal castings, it is essential to choose the right foundry to ensure the highest quality finished product. Finding the right foundry requires careful consideration of a number of factors, including cost, experience, and capacity.
Foundry Definition
Foundries use a variety of processes, including sand casting, die casting, and investment casting. An iron foundry creates parts and components from different materials depending on the requirement of the metal.
Foundries that specialize in cast iron typically use sand molds, while those that specialize in aluminum and other nonferrous metals typically use clay molds.
Types of Foundries
Foundries are typically divided into different types based on the type of metal they use to produce their castings. With the right foundry, you can produce precise metal objects.
Green Sand Foundry
Green sand foundries are gaining popularity as an environmentally friendly alternative to traditional sand casting. These foundries use a combination of clay, sand, and water to produce a mold that is then filled with molten metal.
This type of foundry is a great option for small- and medium-sized businesses. The process is much simpler than traditional sand casting, so it can be easily incorporated into small-scale operations. This makes it a great option for businesses that want to produce castings without the need for large-scale equipment.
Investment Casting Foundry
The process begins with the creation of a wax-based pattern that is formed according to the specifications of the customer. This mixture is heated to high temperatures, which causes the wax pattern to melt and drain away, leaving a negative impression of the desired shape in the refractory material.
Investment casting foundries are highly specialized and require a great deal of expertise and experience. The process is time-consuming and requires close attention to detail in order to ensure the highest quality parts. In addition, the foundry must have the proper equipment, materials, and foundry workers to ensure the quality and accuracy of the finished product.
Centrifugal Foundry
Centrifugal foundry is a form of metal casting process that uses centrifugal force to shape and form a desired object from heated metal. This process is relatively new compared to other metal casting processes.
It is similar to other casting processes, but instead of using gravity to draw molten metal into a mold, centrifugal force is used to shape and form the metal.
The centrifugal foundry process begins with a pattern of the desired object being created, usually out of wax, wood, or metal replica. This pattern is then placed in a centrifuge, which is a device that spins at high speed. The metal is then poured into the centrifuge and the spinning motion of the machine forces the liquid metal outward against the pattern. As the metal cools and hardens, it takes the shape of the pattern.
Casting Process of Molten Metal in Foundries
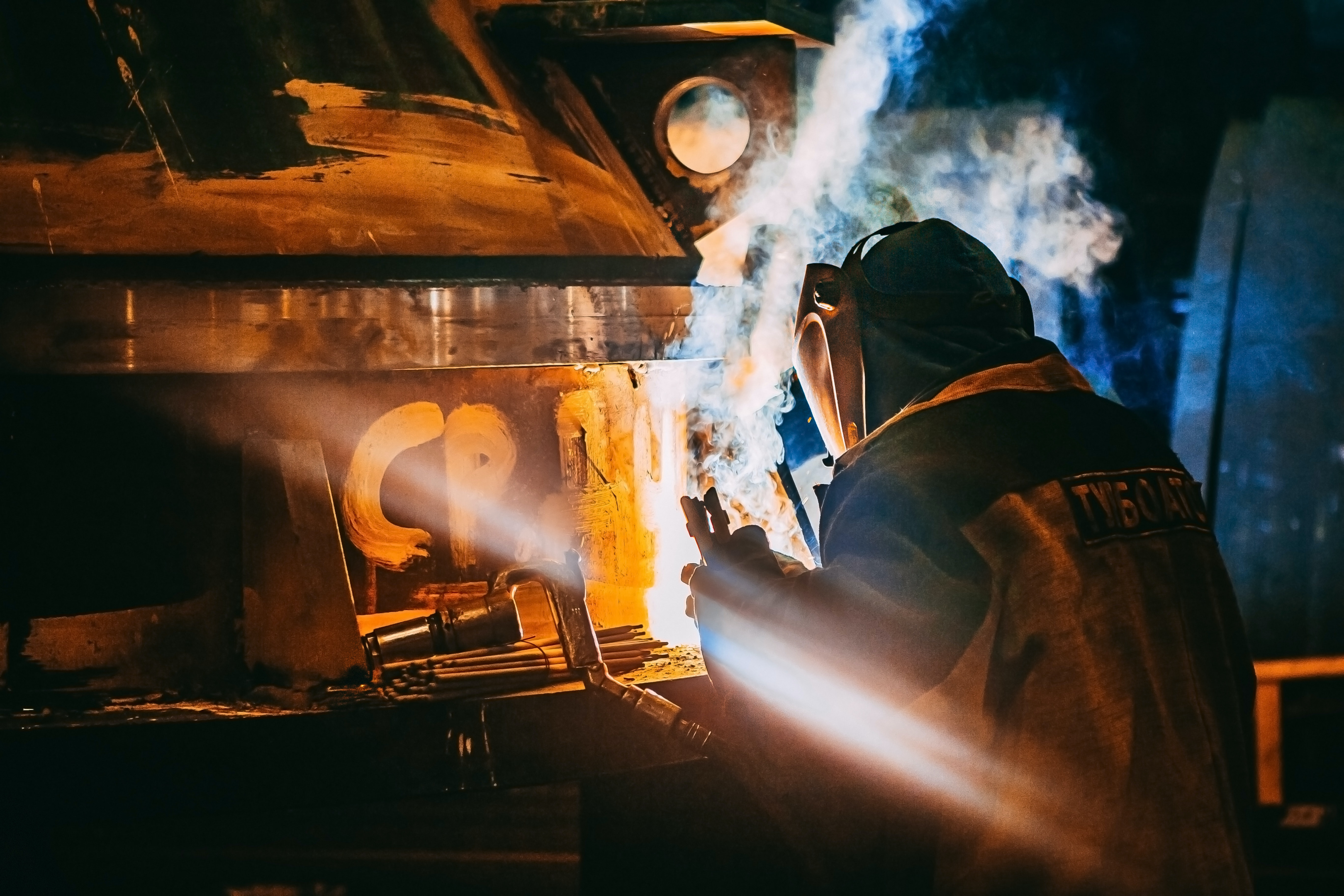
Foundries are an integral part of metal production, as they are responsible for the casting process of liquid metal. The casting process involves pouring molten metal into a sand mold to form a carefully shaped metal.
Creating Mold Cavity
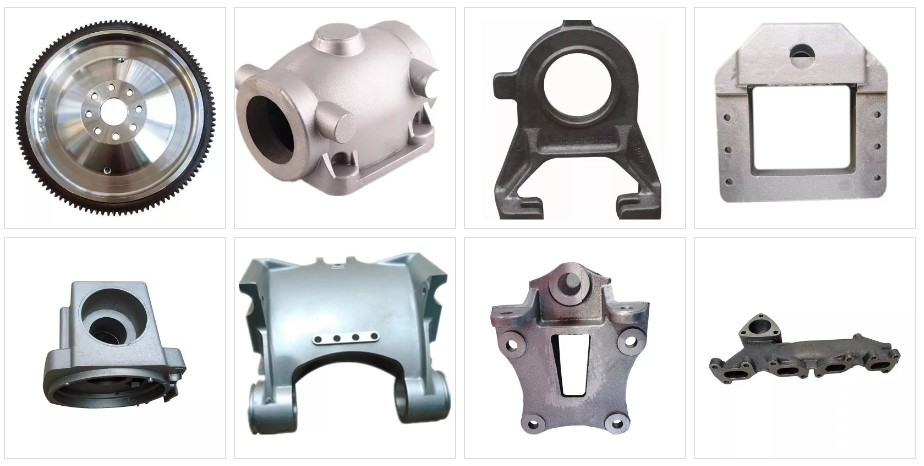
Creating the mold requires careful planning and attention to melting temperatures, as the final shape of the component will be determined by the shape of the mold.
The pattern can be made from wood, plastic, foam, or other materials and should be an exact replica of the shape of the metal objects.
This mold is typically made from silica sand and is composed of two parts. One part is the core making, which is used to make the internal features of the component, and the other is the cavity, which is used to make the external shape of the component.
Melting Metals
Melting metals requires a lot of heat and the right conditions for the metal to reach its melting point. This is done in an induction furnace, in which temperature will depend on the type of cast metal.
Melting metal is a critical part of the process and must be done carefully in order to achieve the desired results. By controlling the temperature and cooling rate of the metal, the shape and size of the casting metal can be achieved.
Pouring Liquid Metal
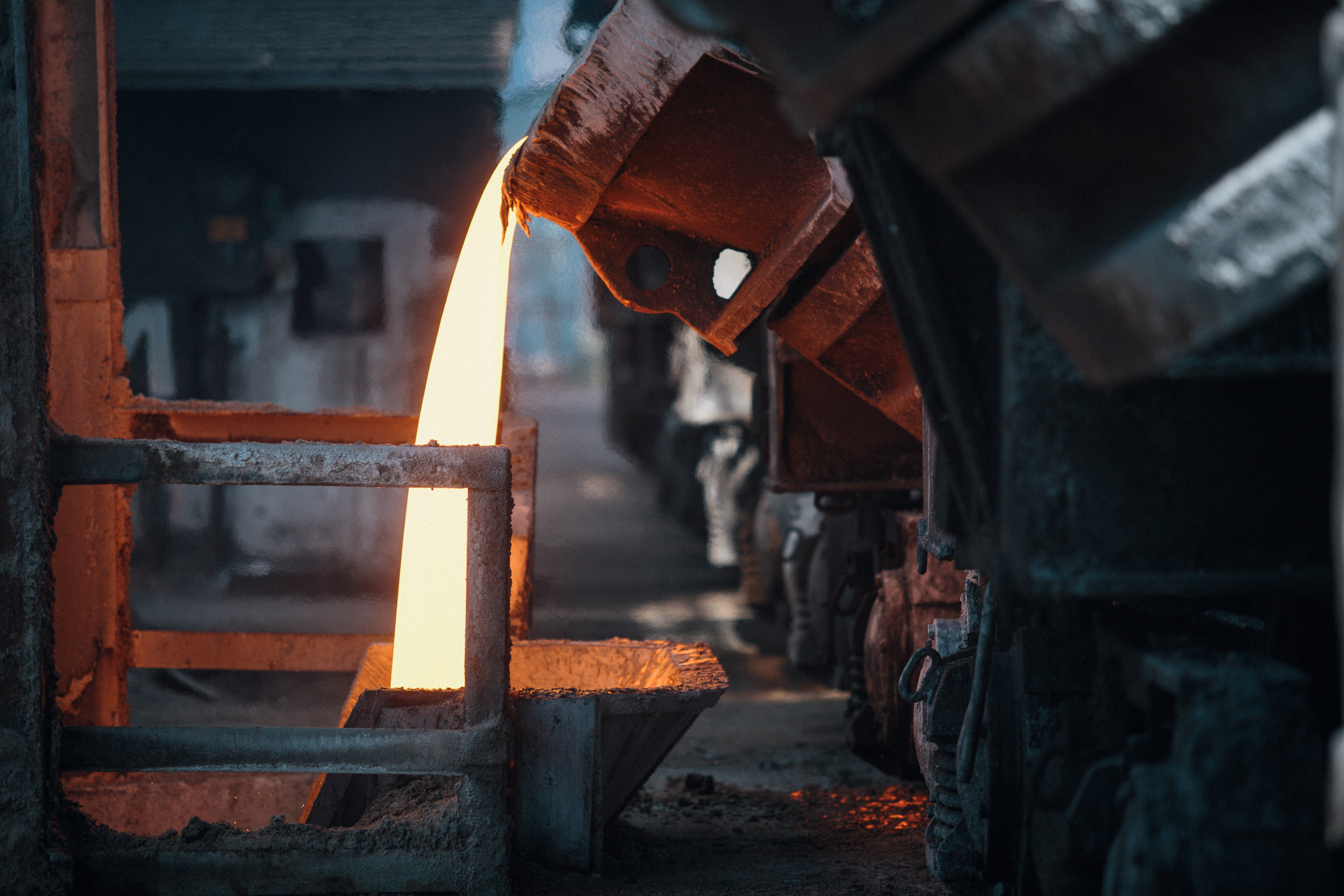
The most important factor in pouring the metal is its temperature. If it is too cold, it will not flow properly and may cause problems such as air pockets or a poor finish. If it is too hot, it can cause the mold to crack or deform. The temperature must be closely monitored throughout the entire process to ensure the best possible results.
It should be done smoothly and steadily, with the aim of achieving a uniform flow. If done correctly, the metal should fill the mold evenly with minimal air pockets or other defects.
Finishing Metal Parts
Once the metal has been cast, it needs to be finished before it can be used. The first step in finishing castings is to remove any excess material or flash. A mechanical method involves grinding or sanding. While chemical methods use acid baths or other solutions that may cause chemical reactions to dissolve the excess material.
What You Can Find in Foundries
Foundries are places where metals and alloys can be melted down and recast into different shapes and forms. In today’s modern world, foundries are used to create everything from car parts to aircraft components.
Melting Metal Furnace
A furnace is a device that uses heat to melt metal or other substances. Foundries use furnaces to melt metal, such as aluminum, iron, steel, and other metals, into a liquid form.
Furnaces come in a variety of shapes and sizes. They can be small and portable, or larger and more permanent. The size of the furnace will depend on the size and type of process that needs to be done. Smaller furnaces are used for casting small objects, such as jewelry, while larger furnaces are used for casting large objects, such as engine blocks.
Machines for Castings
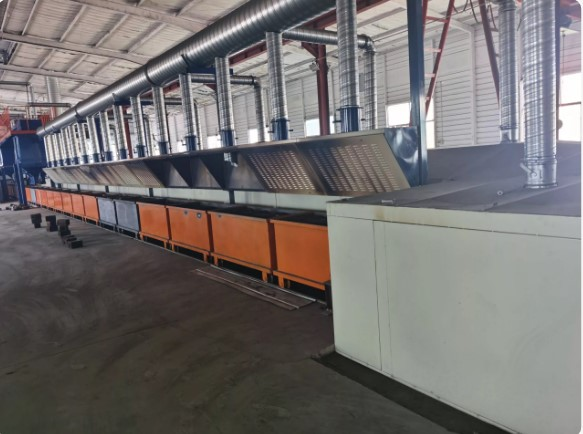
As an integral part of the foundry industry, machines for castings are a key piece of equipment used in almost every foundry. These machines are used to produce parts from a variety of materials such as steel, aluminum, brass, and other metals, as well as plastics and other non-metallic materials.
Finishing Equipment
The most important finishing equipment used in foundries is grinding and polishing machines. This is particularly important for products like engine blocks, which require an extremely precise finish. Polishing is used to give the metal a glossy finish, which can be used to enhance the appearance of the product.
In order to achieve a high-quality finish, many foundries also use vibratory finishing machines. These machines use vibratory action to remove any burrs from the metal and to give it a smooth finish. Vibratory finishing machines also help to strengthen the metal, making it more resistant to wear and tear.
Benefits of Getting Casting-Related Services from Foundries
Skilled Foundry Workers
A foundry worker is responsible for creating and shaping metal casts and shapes used in many industries. Skilled foundry workers must be able to accurately measure and shape the metal, as well as to ensure that the part meets all safety and quality standards.
The expertise of skilled foundry workers is also essential in the production of specialized parts. For example, the production of turbine blades and aircraft engine components requires highly precise and complex molds. Without these people, these parts would not be able to be manufactured with the same level of accuracy and quality.
Safe Manufacturing Processes
Safety is always the first priority in any manufacturing process, and foundries are no different. Foundry workers are exposed to dangerous operations, including hazardous chemicals, dust and noise, and the potential for fire or explosions.
Foundry workers use protective gear, such as face shields, hard hats, and safety goggles for eye protection.
Quality Control
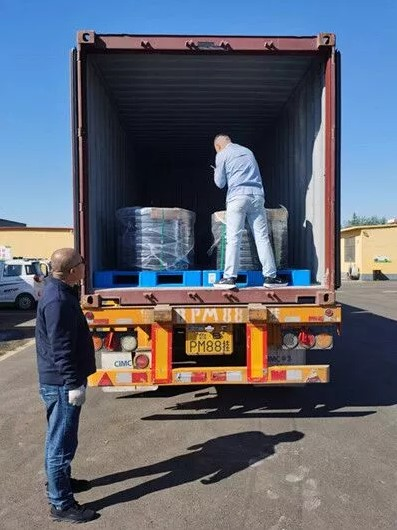
Quality control ensures that the foundry’s products meet customer expectations, while also helping to reduce costs and ensure a safe working environment.
This involves inspecting the molds and components used in the foundry process for any defects such as surface defects, cracks, or other irregularities. Defects can be identified either visually or through the use of X-ray or other imaging techniques.
Once any defects are identified, appropriate corrective measures can be taken to minimize their impact on the metal products.