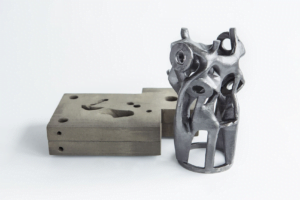

Exploring The Possibilities: Can Sand Casting Cores 3D Printed?
It allows for easy customization of molds and cores. This made the production of complex shapes in small batches or even one-off parts economically possible.
It allows for easy customization of molds and cores. This made the production of complex shapes in small batches or even one-off parts economically possible.
Casting molds may now be made in a way that is both new and more practical thanks to the development of technologies known as additive manufacturing or 3D printing. 3D printed casting molds can be created in a matter of hours, which is important for certain materials that require specific mold properties.
This article will explore the lost foam casting process in detail and discuss its numerous advantages, including design flexibility, cost-effectiveness, and reduced environmental impact.
Kui Tang Foundry is a leading metal casting company located in Weifang, Shandong, China. Established in 2006, we specialize in producing metal castings using high-quality materials for various industries, including engines, automotive, tools, and trains.
With the emergence of 3D-printed lost wax castings, the entire process reduces the costs whem creating a mold. Because of this, it became a preferred method for cost-efficient production.
It eliminates the costs of injection molding, making it a good option for cost-efficient production.
Cast aluminum costs between $1 and $1.10 per pound. Like any other material, cast aluminum can range its current prices per kilo for several reasons.
Anodizing, powder coating, and electroplating are some of the surface finishing options available for aluminum die castings. Each of these procedures offers a variety of benefits that set it apart from the others and help differentiate it from the others.
Die casting is a manufacturing process offers many advantages over other aluminum casting processes. This is mainly because it uses steel mold. It can produce complex shapes with high precision and consistency, high mass production rates and efficiency, and the ability to create parts with excellent strength and durability.
Though both are popular methods for aluminum castings, sand casting vs die cast parts have differences in almost all aspects of the process.
Whether you are a manufacturer looking to optimize your casting process or simply learning more about the two casting methods, this article will provide valuable insights into casting aluminum alloys.
Aluminum castings are highly versatile and useful metals that are important in modern manufacturing. Its unique properties and wide range of applications make it popular in various industries and products.
The chemical composition makes it a highly durable and corrosion-resistant material. Its contact with air forms a thin aluminum oxide layer that adds an extra protection from further corrosion.
This manufacturing process involves injecting molten aluminum using die-casting equipment into a reusable steel mold or die. The result is a cost-effective, high-quality part with excellent mechanical properties and surface finish. This process is best for casting an aluminum alloy.
We will contact you within 1 working day, please pay attention to the email with the suffix “@gmail.com”.