Investment casting and sand casting are almost similar processes, where molten metal is poured into a casing mold. These casting processes started thousands of years ago and are still used in producing metal parts today.
In addition to that, investment casting and sand casting can be used to cast ferrous and non ferrous metals.
Since these are two different casting processes, the advantages and disadvantages of both cannot be compared. They have different benefits and own advantages, so identifying which one is better is not possible, but knowing their difference can be.
In this article, we will discuss each casting method to help us divulge the key differences between the two. A detailed summary of the differences is also included so it will be easy to identify which one is a better option when considering a certain factor.
Investment Casting (Lost Wax Casting)
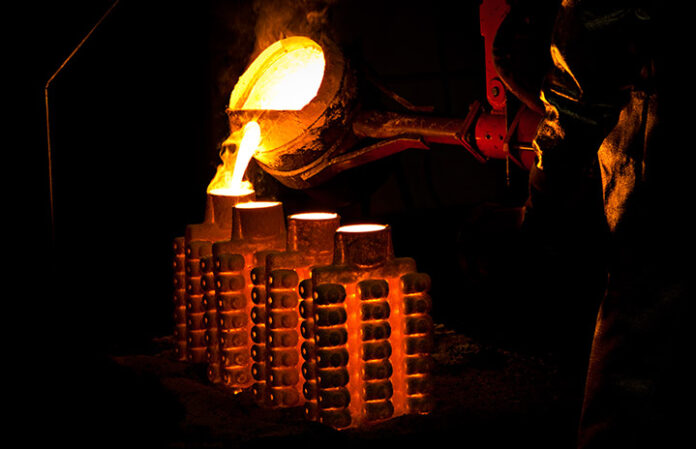
A wax pattern is required to start an investment casting. Also known as the lost wax method, the wax pattern will serve as the mold of the metal casting. This is a precision casting process in which the metal material used in creating the mold is aluminum.
The lost wax method or investment casting method is used in aluminum, carbon steel, and stainless steel.
Investment Casting Process
Investment casting manufacturers place the wax pattern in a liquid slurry to harden and bind the mold. Once the slurry hardens, the manufacturers pour molten metal into the ceramic shell, where the cooling and the solidifying process happens.
As the molten metal cools and hardens, it will follow the shape of its mold.
In mass production of investment castings, the wax runners are assembled in layers that are connected by sprues. Each tree assembly is carefully dipped several times on a refractory slurry.
Like in a single investment casting process, the ceramic shell is heated to remove the wax from the pattern. The wax that has entered the sprues will also be removed during the heating process.
Solid casting blanks will be formed by pouring molten metal and letting it flow within the mold. Completing the process will require breaking the ceramic shell, and the final investment casting parts will be produced with a smooth finish.
Investment Casting Advantages
Because investment casting uses a ceramic shell in molding, which is replaceable, it can be used to produce thin walled parts, even on metal parts that require complex shapes or those that need to add intricate features.
The investment casting technology can create a smooth surface finish right after the mold is taken off. Because of this, you can save time and money in machining. You don’t need to have another process to furnish the final investment casting parts. The finished investment casting can be prepared for delivery.
Investment casting has distinct advantages. However, it still has its drawbacks, especially in size limitation. The molds can only take lower sizes and depths of metals. If you need to cast a larger one, you might need to consider other casting options.
Another drawback of investment casting is the complicated molding cycle. It requires longer preparation and specific equipment. When using this casting process, you need to prepare the molds ahead of time.
Sand Casting: Process, Advantages, and Possible Defects
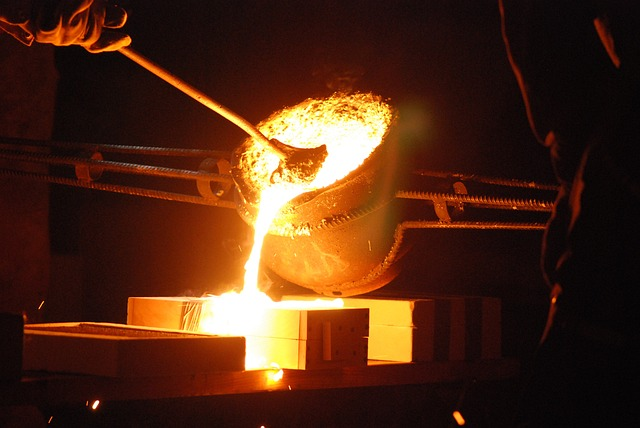
Sand casting is a process where liquid metal is poured over a sand mold. Sand casting parts are made of moistened sand that comes in a clay form. Among other metal casting methods, sand casting is often used in creating metal parts made from non ferrous metals and iron.
This casting method is the top choice of foundries since the raw materials for creating molds for sand castings are easy to source and reusable. Its recyclability can reduce the sand casting cost even for mass production.
Sand Casting: How It Is Done
If the investment casting process uses a wax pattern, sand casting is done with the use of a sand mold. Foundries use green sand, resin, or silica to create the casting sand mold. These are strengthened and bonded to be durable when pouring the molten metal using clay or a bonding agent.
To help the sand mold withstand the flow of the metal, it is required to use a refractory coating. Sand molds are created in parts and are reassembled once they are ready for use.
Once the sand casting process is completed, the sand will be shaken out to take off the finished metal. However, a parting line may be present, which may need a machining process to make the finishing smooth.
Sand Casting Advantage
One of the most widely known benefits of sand casting is the low cost. The raw materials of the molding are easy to find and reusable. Foundries only spend for a new batch of casting sand once the spent foundry sand has been deemed unsuitable for next use. The production cost is relatively low since the process of sand casting is quite simple.
And because the process is simple, the whole production process has a quick turnaround time, especially on mass production. Foundries can create batch after batch.
Though there are much more advantages, sand casting is also prone to having casting defects. It may also have a clip sand or sand wash.
Key Differences of Investment Casting vs Sand Casting
This is a summary of the key differences in properties that you may consider when choosing between investment casting vs sand casting. Each difference will be explained below in this comparison table.
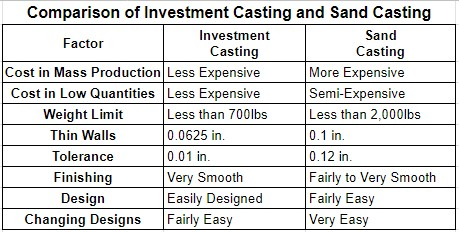
Cost
Investment casting and sand casting require costs. For investment casting, the costs are most evident in the pre-production. The preparation of the shell and wax pattern can be expensive vs sand casting.
As for sand casting, the raw materials in preparing the casting molds is a lot cheaper than investment casting. However, sand casting methods need machining once the metal materials have been finished. The parting line is present, so you need to spend on the machining process to have the perfect surface finish. The finishing job makes sand casting more expensive.
Weight Limit
Investment casting can be used for castings under a certain weight limit, which makes it good for manufacturing small and complex parts. In sand casting, foundries can create castings of all sizes and weights.
Tolerance
As mentioned earlier, investment casting is very flexible when it comes to complex designs. It has a high dimensional tolerance vs sand casting. The properties of the sand molds make sand casting have lower dimensional tolerance.
Surface Texture
Investment casting vs sand casting has a different surface finish because of the make of its mold. Because of the sand grains, expect that the surface finish of sand castings will be rough. However, in investment castings, the raw materials used in preparing the mold can provide a smooth surface once the casting parts are removed from the mold.
It can be used directly, unlike in sand casting, where there are finishing processes that need to be done to achieve the required surface finish.
Ease of Designing
The molds of investment castings are made from a liquid slurry. This means it can be designed in any form. An investment casting can be made with complex structures.
Creating internal parts for sand castings requires more process. The core of the casting parts should be created accurately and properly placed and secured inside the mold. Otherwise, the core may move as the molten metal is poured, which will have an effect on the final casting.
Other Commonly Used Casting Method: Die Casting
The casting requirements will determine the appropriate casting method to use.
Another common casting method is die casting. This casting process is recommended for mass production since the equipment and preparation of the molds can be expensive. Unlike investment and sand casting, it needs high pressure to mold the steel castings.
In choosing the casting process, you should consider some factors, such as materials and turnaround time requirements. Certain metals react to different melting points, tolerance, and other mechanical properties.
Key Takeaways
Investment casting and sand casting have a lot of differences according to their purpose. The casting molds will affect the desired finish.
Investment casting is recommended for small to medium metal parts because it has weight limits. It is also recommended for a metal casting that has a complex structure because its molds can be formed even with a complex design. As for sand castings, its higher weight limit is good for casting larger and heavier metals.
The better casting process to do will depend on the requirements that you need for the finished casting.