Casting and forging are both metalworking techniques that are used to shape metal into complex forms. Both processes involve heating and cooling the metal in a solid state. Casting and forging can both create a certain shape of metals, but there are some key differences between the two that make them suitable for different applications.
The choice between the two processes should be based on the specific requirements of the project.
Casting Process: Using Liquid Metal
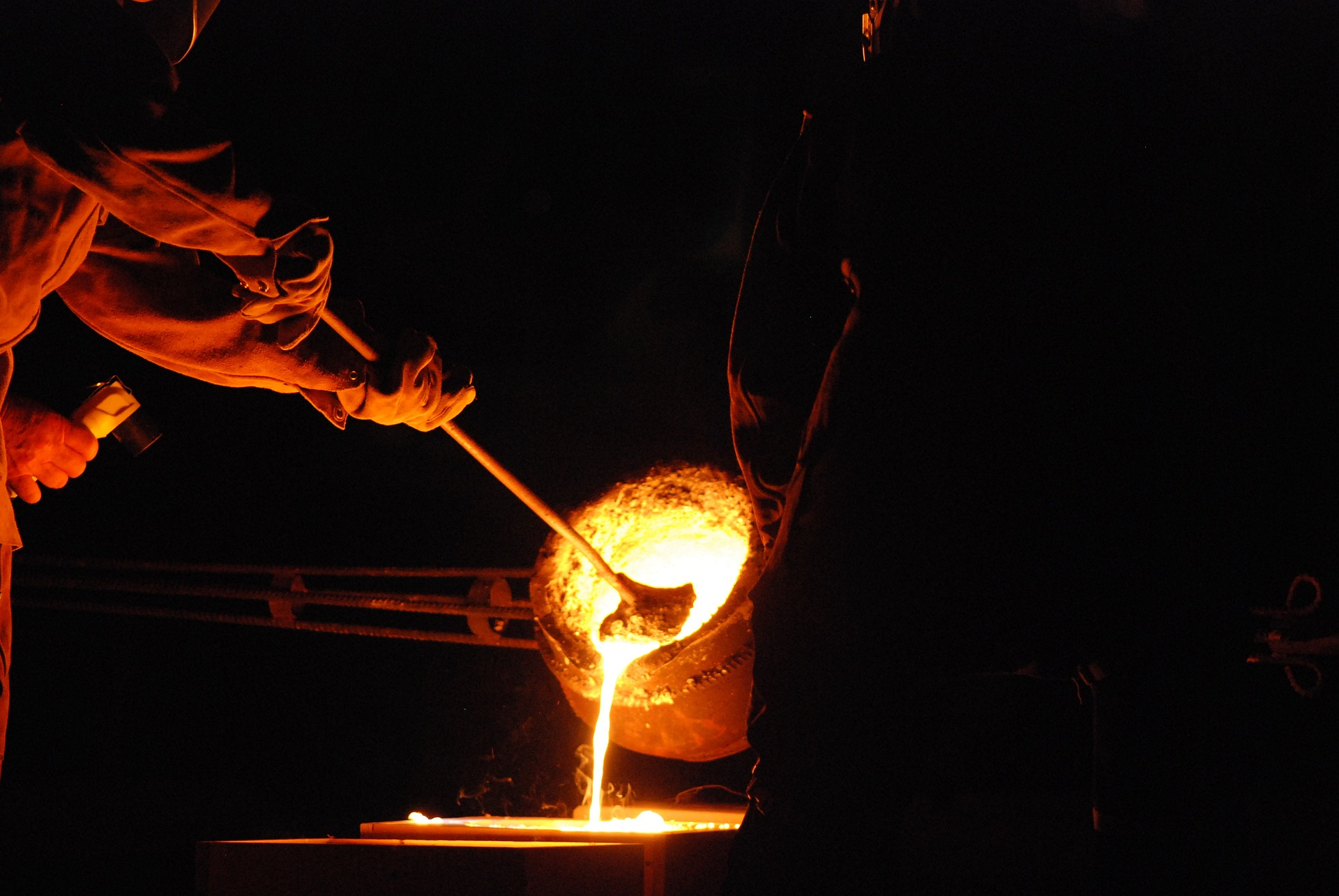
Casting processes melt metal and then pour it into a mold. The molten metal is allowed to cool, and the mold is broken or removed have the finished product.
This process produces a variety of shapes and sizes, from intricate jewelry to large industrial parts. The mold can be made from wood, metal, or plaster, and can be reused to create multiple parts. Casting is a relatively inexpensive process and is often used for larger parts that require more complex shapes and details.
Custom alloys used in casting are aluminum, copper, iron, steel, bronze, and zinc. Each cast iron has its own unique characteristics, such as strength, hardness, heat resistance, and malleability.
Pros and Cons of the Casting Process
Casting metal components is a cost-effective process due to its ability to produce complex geometries and sizes with minimal waste. It is also a flexible process that can be used to produce various cast parts with custom alloys and metals. This cost-effectiveness allows companies to produce metals at a fraction of the cost of other processes.
This process has the ability to produce durable parts that can withstand wear and tear over time and requires excellent yield strength. This durability makes casting ideal for automotive, aerospace, and medical applications where parts must withstand extreme temperatures, pressures, and vibrations.
However, it can lead to long lead times–designing and creating the mold, melting metal, into a liquid state, and pouring the molten metal. This can be a problem for companies that need parts quickly and can cause delays in production.
Porosity is a major concern with casting. Porosity occurs when air is trapped in the metal during the process, resulting in weak spots. Shrinkage and cold pour issues are other issues that can occur when metal components are cast. As the metal cools, it can contract, resulting in a part that is not the desired size.
Casting metal components can also lead to quality assurance issues, such as warping, cracking, or the presence of grain structure. These issues can be minimized by grain refinement and by ensuring that the mold is made correctly. It is also important to use the right casting technique to minimize defects.
Applications of Casting Processes
Metal components made by casting are used in the automotive industry to create a variety of parts, including engine blocks, cylinder heads, and various other engine components. It is also used to make metal beams, columns, and other structural elements with a complex shape.
Casting is used to manufacture medical equipment and components, such as surgical instruments, implants, and prosthetics. It offers the flexibility to create the desired shape and allows for greater strength and durability than other manufacturing processes.
Forging Process: Using Heated Metal
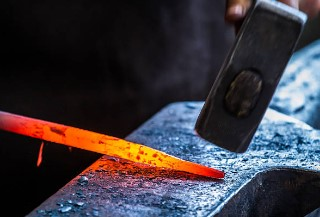
Forging is a manufacturing process in which metal components are physically forced to be formed by pressing, pounding, or squeezing the metal under very high pressure. This process is used to change shape and form forged steel for different applications.
The forging process begins with the selection of suitable materials for the component. Metals such as steel, aluminum, brass, and bronze are often used for forging. The metal is then heated to a temperature that is suitable for forging and creating a new shape.
The heated solid form of the metal is then placed in a hammer or press, where it is subjected to great force. The force causes the metal to deform and take the shape of the die. During the forging process, the metal is subjected to extreme heat and pressure, which helps to strengthen the forged parts and make them more durable.
Pros and Cons of the Metal Forging
Forging metal components is highly versatile. The process can be used to create solid-state applications with a wide range of shapes and sizes, making it ideal for a variety of applications. It is also possible to create components with intricate designs, such as those used in jewelry and decorative items.
Forging metal components produces parts that are incredibly strong and durable. The process of hammering and heating metal under extreme pressure creates a strong bond between the metal molecules, resulting in a part that is incredibly resistant to wear and tear.
One of the major drawbacks of forged parts is it requires specialized equipment and skilled technicians to produce high-quality components. This can make it expensive compared to other manufacturing processes, like machining or die casting.
This process is also time-consuming. Depending on the complexity of the component, it can take several days or weeks to complete a single part. It also has limited design options. Forging is best suited for parts with simple geometries and shapes. More complex designs are more difficult to achieve with this process and can require multiple operations.
Use of Thermal and Mechanical Energy in the Forging Process
The use of thermal energy in this process is important as it allows the metal to become malleable and easier to shape. The thermal energy also helps to remove any impurities or defects.
Mechanical energy is also important in the process. The press or hammer is used to apply pressure in order to shape it. This creates a stronger bond between the molecules in the metal which increases the strength and durability of the product.
Applications of Forged Metal
Forged metal is a popular material used in the construction of many tools, including axes. Axes are an important tool for cutting, splitting, and harvesting wood.
Hammers are some of the most common hand tools made from forging. The heads of hammers are made from a single piece of metal that is heated and then forged into shape. This process creates a strong, durable head that can withstand the force of striking a nail or other object.
Due to its strength, it is also the material of choice for components such as landing gear, engine components, and landing flaps in the aerospace industry. These parts need to be able to withstand the stress and vibration of flight, and forging is able to do that.
Difference Between Casting and Forging Metal Workpiece
casting and forging are two different metalworking processes used to shape workpieces into desired shapes and sizes. Casting is a relatively inexpensive process that is used to create intricate shapes while forging is a more expensive process that is used to create stronger parts.
Both processes involve the use of heat and pressure, but the type of heat and pressure used and the results achieved differs between the two.
Which is Better for Complex Components?
When manufacturing complex components, both are commonly used fabrication techniques. The choice between these processes depends on the type of component being produced and the desired outcome.